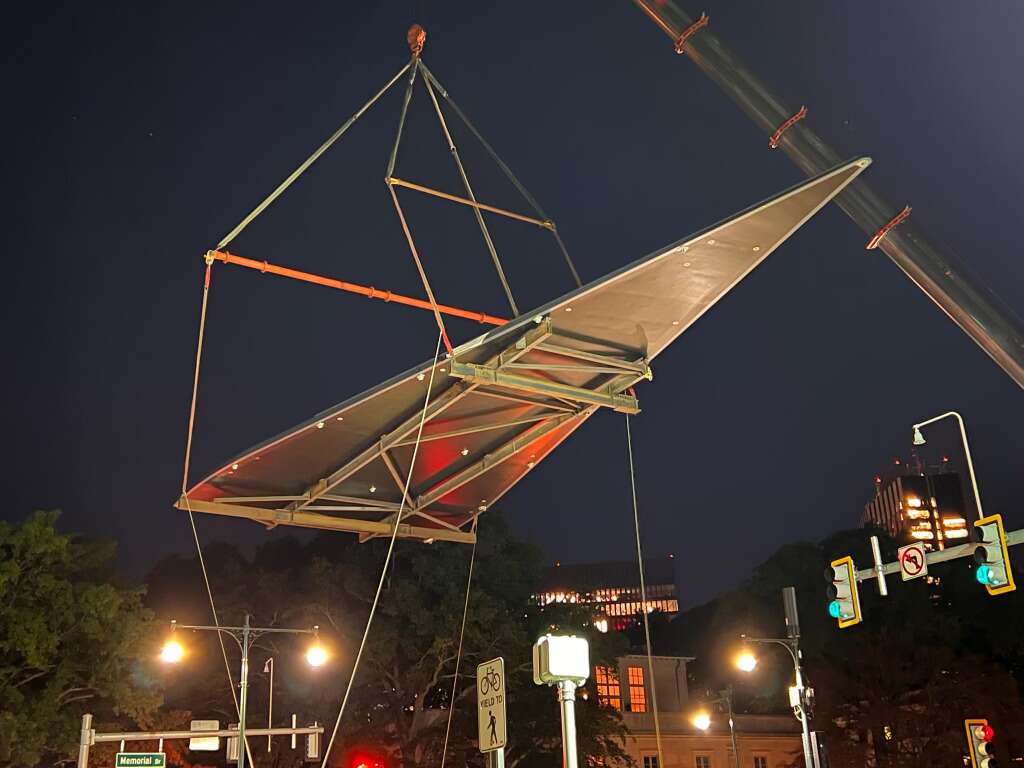
Please do not leave this page until complete. This can take a few moments.
Many know Lyman-Morse Boatbuilding Inc. in Thomaston for its award-winning and innovative power and sailing boats.
For others, the company’s $15 million redevelopment of its Camden marina might have caught their eye.
Perhaps not as well known are the company’s technologies and fabrication divisions, which formed to diversify offerings with projects such as creating historically accurate clock hands for Boston’s landmark Custom House Tower.
More recently, Lyman-Morse Technologies produced and delivered a 160-foot by 32-foot, diamond-shaped composite canopy to be installed over Massachusetts Bay Transportation Authority’s Kendall Square T stop in Cambridge, Mass.
The canopy was constructed of fiberglass and carbon fiber to withstand the natural elements and is not unlike the yachts the company has built since 1978, with telltale design and engineering elements inherent to the semi-custom boatbuilder.
Samir Gupta, head of Lyman-Morse Technologies, and project manager Mike Nile began discussions on the project in 2018, when Lyman-Morse was approached by NADAAA Inc. and Perkins + Will, the project design architect and architect of record for the project, respectively, and both based in Boston.
The two-phase design and build proposal required input and planning from several Lyman-Morse departments.
Structural engineering firm Simpson Gumpertz & Heger of Waltham, Mass., provided the Lyman-Morse team with design criteria and a list of proposed materials for the project that included carbon fiber, fiberglass, stainless steel, aluminum, resin and PET (polyethylene terephthalate) foam for a fire redundant core.
The Lyman-Morse team conducted initial research, with engineers testing their proposed design for manufacturing the carbon fiber canopy via finite element analysis and computational fluid dynamics simulations.
“We had to know how the structure was going to perform in high wind, loaded with snow, and any other outdoor conditions it might encounter,” Nile said in a news release.
The design department determined it could create both halves of the diamond in succession out of one mold, for which it would custom build the tooling.
Via the inhouse computer numerical control machining process, Lyman-Morse fabricated the frames of the mold out of AdvanTech plywood. Lyman-Morse designers were tasked with ensuring the canopy would slot in seamlessly with the support columns.
“Our design team made sure this canopy was laid out precisely,” Nile said. “The canopy is 30 feet in the air and sitting on 26 columns coming from a cement base layer. They had to line up directly into the canopy where we needed to bolt them in, and we had to get it right the first time.”
Nile credited design manager Kevin Houghton in the project.
Anticipating a weight of 15,000 pounds for each 80-foot by 32-foot half, Thomaston’s on-site teams kept busy through fall and winter 2022.
“We set up what’s called a ‘strong back,’ which is basically like the floor joists in a home,” Nile said. “Then we put all the frames on it, we sheathed the whole mold, which is basically the female version of the part, with fiberglass and infused resin into it, then pulled the part up out of it. Just like a boat hull.”
The project was Lyman-Morse’s largest architectural project to date.
Additive manufacturing, or 3D printing, was also used on the project.
“A complicated snow retention system was designed for the top of the canopy,” Nile said. “And we had a design for a snow fence part which runs around the exterior of the canopy, on the top-most outer edge. When it came to the tight radius of the nose, there was some cut and bend, and we didn’t like the overall finish when they were welded together. So, we had stainless steel 3D printed pieces made for both tips of the canopy.”
Underneath the canopy is an interactive LED installation, engineered by MIT-founded SOSO Limited and powered by open-source code, that features rotating illumination in contrasting hues.
Moving the canopy from Thomaston to Cambridge included hiring two barge companies; choosing an installation date that didn’t conflict with boat races, road races and outdoor events; shutting down roadways; and acquiring permits from private, municipal and state organizations.
The canopy covers an area close to 3,000 square feet.
“It just all fell in place really well,” Gupta said. “Mike [Nile] had brilliant planning throughout and really, coordination was the key.”
“When the last bolt went in and the leading manager at Turner Construction, the general contractor, just looked at us, the feeling was ‘I can’t believe we pulled it off perfectly!’” Nile said with a laugh.
The Giving Guide helps nonprofits have the opportunity to showcase and differentiate their organizations so that businesses better understand how they can contribute to a nonprofit’s mission and work.
Learn MoreWork for ME is a workforce development tool to help Maine’s employers target Maine’s emerging workforce. Work for ME highlights each industry, its impact on Maine’s economy, the jobs available to entry-level workers, the training and education needed to get a career started.
Learn MoreThis special publication examines the innovation infrastructure in Maine and the resources available to help entrepreneurs at the various stages of their journey.
Learn moreThe Giving Guide helps nonprofits have the opportunity to showcase and differentiate their organizations so that businesses better understand how they can contribute to a nonprofit’s mission and work.
Work for ME is a workforce development tool to help Maine’s employers target Maine’s emerging workforce. Work for ME highlights each industry, its impact on Maine’s economy, the jobs available to entry-level workers, the training and education needed to get a career started.
This special publication examines the innovation infrastructure in Maine and the resources available to help entrepreneurs at the various stages of their journey.
In order to use this feature, we need some information from you. You can also login or register for a free account.
By clicking submit you are agreeing to our cookie usage and Privacy Policy
Already have an account? Login
Already have an account? Login
Want to create an account? Register
In order to use this feature, we need some information from you. You can also login or register for a free account.
By clicking submit you are agreeing to our cookie usage and Privacy Policy
Already have an account? Login
Already have an account? Login
Want to create an account? Register
This website uses cookies to ensure you get the best experience on our website. Our privacy policy
To ensure the best experience on our website, articles cannot be read without allowing cookies. Please allow cookies to continue reading. Our privacy policy
0 Comments