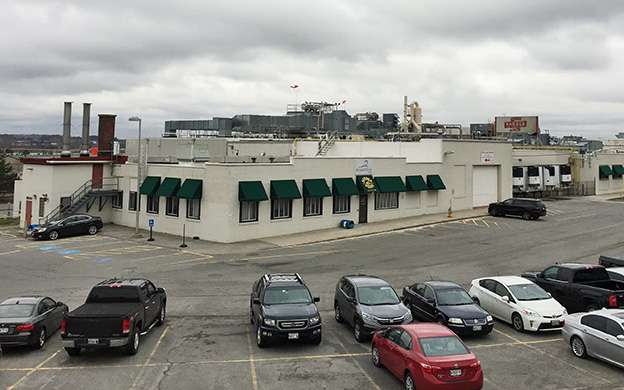
Please do not leave this page until complete. This can take a few moments.
Testing is underway for 400-plus employees at Portland's Tyson Foods plant, the first business in the state that's not a congregant living setting to report a COVID-19 outbreak among employees.
The company is implementing safety and health measures at the former Barber Foods plant on St. John Street, similar to those Tyson is working on at plants across the country, as it remains closed until all employees are tested, said spokesman Worth Sparkman.
Of 96 employees tested by Monday afternoon, 17 had tested positive for COVID-19, including the 12 initial cases reported last week, according to Maine CDC Director Nirav Shah. The CDC confirmed to Mainebiz this morning that it's the first outbreak at a business that isn't a congregant living setting in the state. Most of the state's outbreaks have been at rehabilitation or senior care centers.
The company closed the plant for cleaning and employee testing after the outbreak was discovered and it will remain closed until all employees are tested and results are available, Sparkman said.
“While the plant is idle, we are performing a deep clean and sanitization of the facility and are continuing to work closely with the Maine CDC to ensure our efforts meet or exceed state and national guidelines," he said.
Sparkman said the company won't comment on specifics, including the number of cases. "Since this is an ever-changing situation, we’re not sharing specific numbers in Portland," he said. "We will work with Maine CDC and an outside medical contractor to conduct COVID-19 testing for all of our team members in the coming days.
"The health and safety of our team members is our top priority, and we take this responsibility extremely seriously," he said.
Nationally, Tyson has contracted with Arizona-based Matrix Medical Network to provide testing and other health support at "select" plants across the country, Tyson announced Friday. Sparkman wouldn't comment on whether Matrix is doing the Maine testing.
Many of the employees at the Portland plant, which produces chicken products, are members of the city's immigrant community, and Shah said that Maine CDC is working with community representatives to help with contact tracing — the practice of determining who those who test positive had contact with over the two weeks prior to testing positive.
Shah said the work with immigrant community representatives is key, because there's a concern some may avoid CDC overtures, "and continue to be unwell."
Tyson, over the past several weeks, has dealt with larger outbreaks at meatpacking plants across in Iowa, Indiana, Washington and other states. Many of those plants have also been closed while the company tests employees and enhances health and safety measures.
"Education is an important part of our efforts and we’re doing our best to ensure our team members understand risk factors so that they can stay safe at work and at home," Sparkman said.
Specific measures being taken at all Tyson plants include:
Tyson Foods Inc. (NYSE: TSN), of Springdale, Ark., acquired AdvancePierre Foods Holdings Inc., the parent company of Barber Foods, in 2017. At the time, Barber said on its website that it employed 280 people of 36 nationalities.
Barber Foods, originally Barber Beef and Poultry, was founded in 1955 as a meat truck owned by Gus Barber, the son of Armenian immigrants. Barber, who died in 2008, expanded that into the chicken production plant on St. John Street.
The Giving Guide helps nonprofits have the opportunity to showcase and differentiate their organizations so that businesses better understand how they can contribute to a nonprofit’s mission and work.
Learn MoreWork for ME is a workforce development tool to help Maine’s employers target Maine’s emerging workforce. Work for ME highlights each industry, its impact on Maine’s economy, the jobs available to entry-level workers, the training and education needed to get a career started.
Learn MoreThis special publication examines the innovation infrastructure in Maine and the resources available to help entrepreneurs at the various stages of their journey.
Learn moreThe Giving Guide helps nonprofits have the opportunity to showcase and differentiate their organizations so that businesses better understand how they can contribute to a nonprofit’s mission and work.
Work for ME is a workforce development tool to help Maine’s employers target Maine’s emerging workforce. Work for ME highlights each industry, its impact on Maine’s economy, the jobs available to entry-level workers, the training and education needed to get a career started.
This special publication examines the innovation infrastructure in Maine and the resources available to help entrepreneurs at the various stages of their journey.
In order to use this feature, we need some information from you. You can also login or register for a free account.
By clicking submit you are agreeing to our cookie usage and Privacy Policy
Already have an account? Login
Already have an account? Login
Want to create an account? Register
In order to use this feature, we need some information from you. You can also login or register for a free account.
By clicking submit you are agreeing to our cookie usage and Privacy Policy
Already have an account? Login
Already have an account? Login
Want to create an account? Register
This website uses cookies to ensure you get the best experience on our website. Our privacy policy
To ensure the best experience on our website, articles cannot be read without allowing cookies. Please allow cookies to continue reading. Our privacy policy
0 Comments