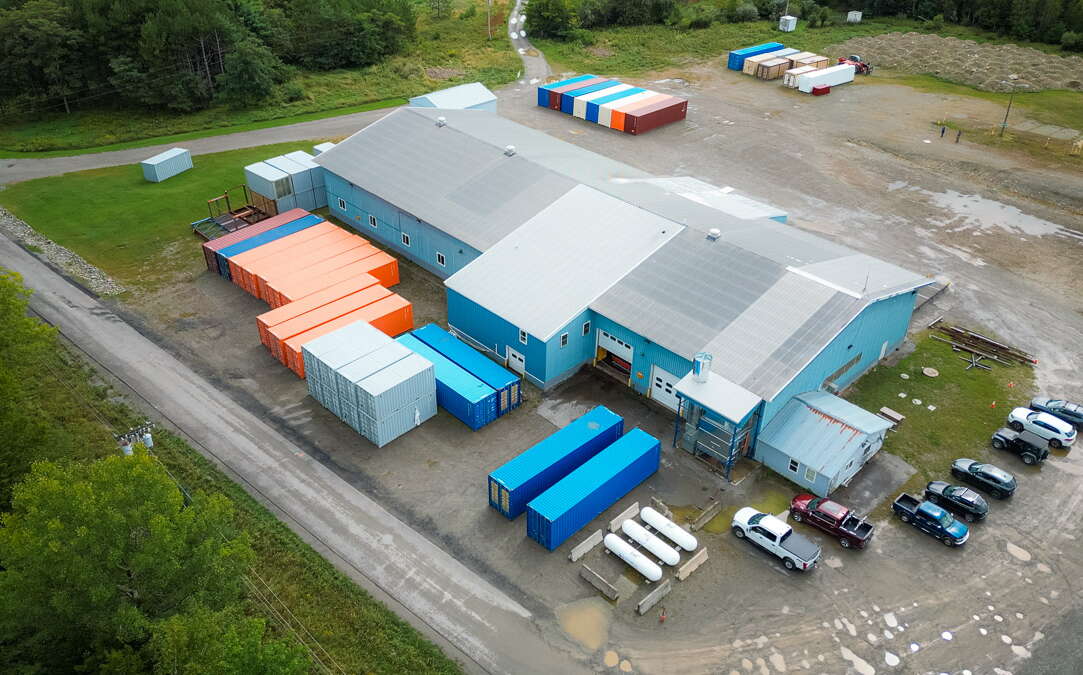
Please do not leave this page until complete. This can take a few moments.
Down an inconspicuous side road in the Penobscot County city of Old Town, in a large but unremarkable former truck garage, big things are going on for the global shipping industry.
A startup called Global Secure Shipping is making a new type of shipping container built from high-strength composite materials embedded with advanced sensors designed to enable government and commercial companies to fight theft and tampering.
The container commercializes patented technology resulting from years of Department of Homeland Security-funded research and development at the University of Maine’s Advanced Structures and Composites Center and the Georgia Tech Research Institute.
“The company and the technology is being looked at by the shipping industry with a lot of interest,” says Robert Lindyberg, CEO of Global Secure.
Lindyberg recently returned from a National Defense Transportation Association and U.S. Transportation Command co-sponsored meeting in Orlando, Fla., where he met with shippers and government agencies. He started traveling to government agency and commercial shipping conferences in 2019 and has been ramping up the road show since 2021.
“There’s a great deal of interest in utilizing the technology to reduce theft and pilferage and to reduce tampering,” he says.
The project dates to a solicitation issued 20 years ago by the U.S. Department of Homeland Security Advanced Research Projects Agency for secure shipping technologies.
UMaine’s Advanced Structures and Composites Center was one of a number of the winning respondents and set about designing and testing secure containers.
Global Secure was established as a spinoff company in 2018 to commercialize production. Outgrowing its lab space, it moved two years later to the 17,500-square-foot building on city-owned land at 122 Penny Road, where logging trucks were once housed and maintained but had been vacant for a couple of years.
A year later, the first-generation container passed various tests with flying colors. To date, Global Secure has produced 32 shipping containers for the federal government and has 20 employees.
Now Global Secure and the city of Old Town are collaborating to build a second 15,000-square-foot building at the same location, where ramped-up production will begin with a $3.2 million Department of Homeland Security contract for the construction of 48 secure shipping containers.
The city is covering the $3.9 million construction cost and will lease the building to Global Secure to accommodate expansion.
The city’s collaboration with Global Secure dates to 2018. “We worked with Bob and his team to understand where they started,” says E.J. Roach, Old Town’s director of economic and community development. “This has been a 20-year project at UMaine, and it needed space to grow. Manufacturing jobs, we feel, are vital to the mix of our economy in Old Town.”
Sitting on the edge of the northern forests and the Penobscot and Stillwater rivers, Old Town was once a major supplier of lumber in the U.S. A long-time presence has been the Old Town Mill, which was acquired by ND Paper in 2018.
But the mill industry has been through ups and downs. “We have spent decades celebrating when a mill opens, and then being upset when a mill closes,” says Roach. “So we’re trying to diversify some of our manufacturing jobs. Global Secure fit into the mix.”
He adds, “We found their project met the solid criteria you look for in someone who’s in it for the long term and is going to create good jobs. We saw that these guys had a solid plan. We were going to step up and help them to get from point A to point B.”
An estimated 250 million containers are transported across the seas with over $7 trillion worth of goods, according to the World Shipping Council.
Although the pandemic disrupted ocean transport, leaving containers tied up in storage and vessels stuck outside ports, “we still moved more volumes than ever, and kept supply chains moving,” says the council. “As demand normalized and capacity was freed up, rates and service levels have come back to pre-pandemic levels.”
But with all that valuable cargo, theft is a multibillion-dollar problem.
In the U.S., cargo theft taking place anywhere in the transportation pipeline — including containers and facilities related to water, land and air transportation — costs $15 billion to $35 billion, according to the National Insurance Crime Bureau.
UMaine’s Advanced Structures and Composites Center’s team, led by Anthony Viselli, saw that the composites construction method was a great way to embed ultra-thin, high-tech detection technology within the panels that comprise the shipping container itself.
Composites would also be lighter than steel, yet just as strong and visually indistinguishable.
The embedded sensor system detects penetrations as small as one inch. There’s a door-opening detection system and a two-way communications system for real-time tracking and monitoring.
The system was developed by the Georgia Tech Research Institute, also through funding from Homeland Security’s Advanced Research Projects Agency.
The hardware and security system are designed to be modular and expandable so that additional security features and sensors can be integrated into the basic system.
A proof-of-concept scale model resulted in further Homeland Security funding for full-scale development. Once the expansion is up and running, Global Secure will produce 1,000 40-foot containers per year.
In all, the project has received $30 million in government funding.
Lindyberg is a civil structural engineer who arrived at UMaine as one of the first graduate students at the Advanced Structures and Composites Center, in 1994. By 2011, he was the center’s assistant director. He eventually left to join the private sector in North Carolina.
“Then I had the opportunity to come back here in 2019 to take this on,” he says. “I jumped at it.”
On a recent autumn day, he took Mainebiz on a tour of operations.
The facility includes precision molding capabilities, computer numerical control laminate cutting machines and modern process controls. Composite layup equipment includes resin injection pump and vacuum bagging system. Long rails in one area allow containers to be moved in and out of the building. Floor racks are loaded with rolls of fiberglass fabric and wall-mounted racks are draped with completed fiberglass-and-sensor assemblies, sorted by various sensor configurations.
Lindyberg points out a section of steel. Offering an example of one of the countless problems to be solved in the container’s development, he explains that the type of steel, often used for outdoor construction, comes with a skiff of oil and is designed to develop a rust patina to protect it from the elements. For composite panels that needed to be bonded adhesively to steel frames, the oil was an impediment.
The team tried sanding, grinding and solvents to remove the oil. Nothing worked. The answer? An online home remedy.
“We found out that soaking them in vinegar was the best way to go,” says Lindyberg.
The use of layered fiberglass fabric allows an electronic sensor system the thickness of aluminum foil to be sandwiched in the middle throughout the length and width of each panel.
In a process called “light resin transfer molding,” panel construction starts with laying fiberglass fabric on a rigid male mold, layering on the sensor system, then more fiberglass. The assembly is loaded onto a female mold and sealed using vacuum pressure, which draws resin in for thorough saturation.
The panels are bonded to steel frames, paint is applied and additional electronics go in to allow the security system to communicate to the cloud, allowing the container’s location and status to be tracked on an app.
Drilling or cutting through a panel breaks the sensor’s strands and sets off an alarm.
Today, Global Secure is the exclusive producer of the only International Organization for Standardization-certified intermodal shipping containers in the world that provide six-sided security and worldwide tracking.
The majority of contracts are with the government. Containers in commercial trials with shippers and freight forwarders are generating interest.
“They’re using the containers we’re supplying on a trial basis, to see how effective it is at detecting theft,” he says. “We’re very much gathering data on that.”
Compared with a standard container’s cost of several thousand dollars, the high-tech model is expected to be three to five times more. But customers have indicated a willingness to foot the bill, says Lindyberg.
Commercial operations will “get that back in one or two foiled theft attempts,” he says. “If you’ve got half a million dollars of electronics or pharmaceuticals in a container and you foil a theft attempt, that’s quite a bit of savings.”
The expansion recently broke ground and is expected to be operational by summer, with the potential to generation 80 more jobs.
Despite Maine’s generally tight labor force, Lindyberg expects to find the employees needed.
“We offer competitive wages and benefits,” he says. “In addition, we’re able to bring in folks with a modest skill level and training, and we train them here ourselves. So far, everyone working here is local.”
The company also sources materials locally as much as possible.
The project could result in several hundred indirect jobs, says Roach. And the city is planning further development on an additional 160 acres around Global Secure, with the goal of growing the manufacturing base.
The city receives queries from companies, local and beyond, looking for industrial space.
“Old Town doesn’t have a lot of vacant space available,” says Roach. “So we’ve talked for quite a while about developing an energy and enterprise park.”
The plan is to continue to invest in infrastructure improvements for the acreage.
“Our hope is that Global Secure will be the anchor tenant and be a beacon that will show others what it takes when you have the right players and the right support,” says Roach.
Lindyberg cautions that the overall effect of the technology on the shipping industry remains to be seen, as it’s adopted and utilized.
“But the potential is there to revolutionize secure shipping,” he says.
0 Comments