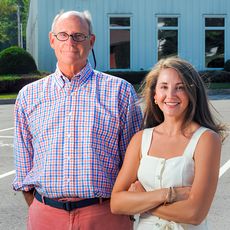
Please do not leave this page until complete. This can take a few moments.
Timothy Templet’s phone started ringing in mid-March last year and hasn’t stopped ringing since.
Puritan Medical Products Co., the century-old manufacturer of medical swabs in Guilford, found itself in the center of the chaos of the global pandemic and one of only two companies in the world able to produce the testing swab needed to diagnose COVID-19.
The calls that began on Saturday, March 14, 2020, were unlike any Templet, Puritan’s co-owner and executive vice president, has ever fielded before: The White House Covid-19 Response Team; Brett Giroir, the U.S. Assistant Secretary for Health; the U.S. Food and Drug Administration, and U.S. Sens. Susan Collins and Angus King, among others.
What additional products did Puritan have? How fast can you make more? Hundreds of millions more?
“You don’t have a lot of time to think about it. You react. We’re small — we can react when we have to. We can have all the valuable people in one room and do many things at once,” Templet says.
Immediately, Puritan began working at warp speed. Days consisted of 3 a.m. conference calls and the pace accelerated from there, Templet says.
“In a pandemic, the hour of the day does not matter. We were working 24 hours a day, basically. Time didn’t mean anything to us,” Templet says.
Founded 102 years ago, during another pandemic, Puritan began as a toothpick maker. It later expanded its product line and in 1928 introduced its first medical product — the tongue depressor, which it still makes today. It now makes roughly 1,200 products, including 65 types of swabs.
Before the pandemic, Puritan had annual revenues of $45 million. Templet declined to disclose Puritan’s profits or discuss its finances during the past year, other than to say Puritan “managed quite well.”
Last year, Puritan received $126 million in government contracts through the Defense Production Act and the Cares Act that helped it build two plants in Pittsfield, which supplemented its existing manufacturing facility in Guilford.
Puritan had to do a lot at the same time: get equipment drawings in place and find a way to build new manufacturing machines, secure a building, find a contractor, hire hundreds of people, source raw materials and keep production going on its other products.
The government put Puritan and shipbuilder Bath Iron Works in touch to solve the machine problem.
BIW says it was originally contacted by Air Force Major General Cameron Holt, Director, Air Force Acquisition COVID-19 Task Force and the Deputy Assistant Secretary for Contracting. The task force learned about BIW capabilities from Peter Navarro, director of trade and manufacturing policy, in his role as National Defense Production Act policy coordinator.
“The U.S. Air Force, which coordinated contracts under the Defense Production Act, determined Bath Iron Works was uniquely capable to build the necessary machines within the required time frame,” BIW says.
Puritan took one of its wrapping machines, as well as design plans, to BIW so the shipbuilder could work directly from the machine and deconstruct it in order to build 30 more.
“It was the first time in our career to have our proprietary machines built by anyone but ourselves,” Templet says.
One of Puritan’s engineers would go to BIW every week to coordinate on the project, Templet says.
A wrapping machine typically takes about one year to manufacture. BIW made 30 in two months.
“This was a unique project for a once-in-a-lifetime health crisis that demanded our specific expertise in sourcing materials and components and crafting precision equipment,” said BIW spokesman David Hench. “We focus all our energy on serving our Navy customer and this unique circumstance was due to the unprecedented challenges of the pandemic.”
BIW had more than 300 employees working on the Puritan projects. The shipbuilder says it also turned to more than 10 other Maine businesses to provide materials or make specialized parts for the machines.
For the Pittsfield plants, Puritan worked with Cianbro Corp., which operated two crews working 12-hour shifts to keep construction going around the clock to get the first facility up in running in eight weeks.
Internally, Puritan put manufacturing engineer Derek Mckenney in charge of the first Pittsfield plant.
“I would have never thought he had all that in him,” Templet says. “He’s a bright young man, 20-something. He built a building within a building and got it done.”
At the first location, 129 N. Main St. in Pittsfield, Cianbro had a design, engineering and construction crew of 740 people devoted to the building. Of that crew, 170 were Cianbro employees and the rest were subcontractors.
“It was amazing that on both projects people understood how important the swab facilities were to the nation and to Maine. It’s amazing to see how the collaboration came together,” says Richard Brescia, Ciabro’s senior vice president.
Cianbro says it first got a call from Puritan in late April and the construction firm had three hours to submit its bid for a factory that needed to be producing swabs by July 1.
“The word ‘can’t’ is not in our vocabulary. We just don’t breathe that word,” Brescia says. “The state of Maine and the community pulled together. It showed what we can do here.”
The project consisted of a 100,000-square-foot, abandoned smoke detector plant in Pittsfield. Lead paint and asbestos forced the firms to reduce the building to its steel skeleton and start from scratch. Normally the overhaul and rebuild of the factory would have taken more than 18 months, the company says. Puritan and Cianbro did it in eight weeks.
While the Puritan project was unique in some ways for Cianbro, especially the pace and high-profile nature of the cause, the company was able to build on its years of experience to get it done.
“The key is making sure the communication — hour by hour — is clear,” Brescia says.
“The hardest part was that the schedule was very challenging. And every single day things might change: the condition of the building, the machine layout. We had to have a solution for all of that. We very quickly came up with a solution and moved on and forward,” Brescia says. “The uniqueness of the project itself was hard. Old buildings being turned into state-of-the-art, medical grade production rooms,” Brescia says.
The second facility in Pittsfield, at 206 SAS Drive, was a former 79,000-square-foot San Antonio Shoemakers building. That project needed a new roof and exterior walls, but was on a less frantic schedule than the first factory that had to be up and running immediately, Cianbro says.
Templet says Puritan has received a request from the government for a fourth plant, in addition to Guilford and the two in Pittsfield. Details are still being worked out. BIW and Cianbro declined to comment on whether they would be involved in making machinery or working on the fourth building.
With the new factories, Puritan can make more than 140 million COVID swabs a month, a 30-fold increase in a year.
Getting the raw materials to make the swabs was not difficult, Templet says.
“The whole world was in peril. People reached out to us from all over the country,” Templet says. “That was a shining light in the pandemic.”
Hiring enough people to keep the plants running, however, was a challenge, Templet says.
Puritan worked with KMA Consulting, a human resources firm, to vet candidates and help Puritan do final interviews.
“It’s been a challenge. You never know — you think you have a good candidate and then they don’t come back,” Templet says. “We’re always looking for more workers. You always are going to have to hire more than you need so you can keep the machine running.”
“The most visible thing was the dedication of our workers. The can-do attitude. I’m very proud of them. We had school teachers and professions offering to come here to work extra shifts because they wanted to be part of something bigger. In today’s world, that’s hard to find sometimes. That warm and fuzzy feeling. But during this we had the sense that we are Americans and we’ll pull together and make it right,” Templet says.
Puritan now employs 1,300 people, up from about 500 before the pandemic.
The company still has a few headaches to sort out.
Puritan’s rival, Copan Diagnostics of Italy, previously sued Puritan alleging patent infringement over five flocked swabs. The companies have temporarily sidelined the legal issues due to the pandemic.
Eventually the pandemic will end, but Puritan still expects to remain very busy.
“The rest of 2021 will be very busy; 2022 will be very busy, as well,” Templet says. “This is the new world for us. Testing for viruses and bacteria will not go away.”
Templet also sees an upswing in demand for self-collection kits and self-screening tests.
“The United States embraces with open arms self-collection. Other countries don’t embrace it, but in the U.S., the self-collection model is here to stay,” Templet says.
0 Comments