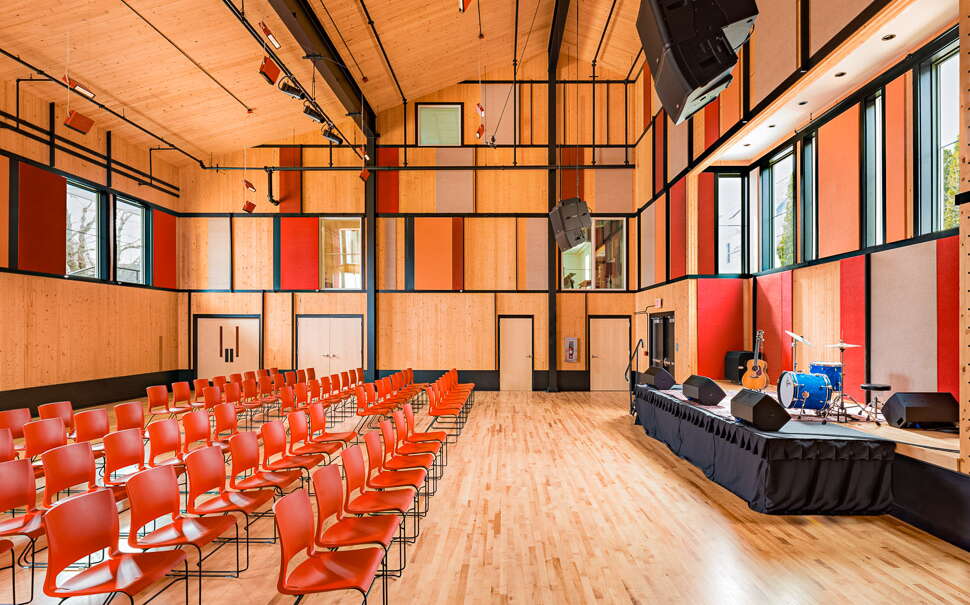
Please do not leave this page until complete. This can take a few moments.
When the Portland Museum of Art starts construction on its $100 million expansion, it is expected to showcase an innovative building product that’s gaining popularity here but is not yet produced in Maine: mass timber.
The 60,000-square-foot building is designed by Portland, Oregon-based LEVER Architecture to be “a mass timber super structure,” says the builder, Matt Tonello of Consigli Construction. It will be “all mass timber above the foundation.”
The museum’s director, Mark Bessire, has become an advocate for the product, saying its use in the new wing will create a welcoming environment, which he says is rare for a museum.
“Museums look too corporate,” he said at conference in November. “They look like banks. And there is no more friendly material than [what you see] walking into a mass timber building.”
“We want to have a mass timber art museum,” he said. The Williams College Museum of Art could be the first.
“We want to be the building that advocates for this because we think more people need to know about the possibilities and how we can use our natural resources more,” Bessire said.
The use of the mass timber is starting to find more favor among architects, engineers and builders in Maine who value its structural stability, light environmental footprint and the wood’s natural beauty.
Also contributing to its increasing adoption is the product’s fabrication, which facilitates a more simplified and cost-effective building process, when compared with the use of steel and concrete.
Advocates see great potential for its use in housing development, as building codes now accept mass timber for structural use, and the speed of construction with the material makes a taller build, with more apartments per lot, more economically feasible.
The term "mass timber" refers to a constellation of engineered wood products — cross-laminated and glulam are the most commonly used — which are engineered from layers of select woods chemically (with glue) or mechanically fastened together to create larger, stronger building materials.
Glulam and nail-laminated beams and columns are utilized for structural support, in place of steel or masonry.
Cross-laminated panels are used for floors, walls and ceilings. They’re favored too for elevator shafts and stairwells, where swapping them for conventional materials speeds construction times on those foundational project pieces. Curtis Thormann, vice president of operations at Freeport-based Zachau Construction, says the savings are considerable — from a month’s time with a masonry shaft to a matter of days with mass timber panels.
Zachau employed mass timber for its first project in 2020 at Portland’s Wessex Woods and then in two more housing complexes, two commercial buildings, and in 317 Main Community Music Center’s 5,000-square-foot addition in Yarmouth. Zachau has three more projects on the horizon that will use mass timber along with conventional products.
To date, most builds in the U.S. that incorporate mass timber combine it with traditional materials in a hybrid structure.
There are varying opinions on the cost of the material. Thormann says Zachau has found it to be slightly more expensive than a conventional steel and concrete building, but typically much more expensive than a traditional wood-framed building.
“In our market, four- to five-story wood-framed structures are common for multi-family structures and mass timber has not offered an affordable alternative,” says Thormann. “With construction pricing at the highest it’s ever been, the market is driving to build as efficiently as possible which usually eliminates the ability to fully incorporate mass timber into the design.”
Thormann finds though that he can build faster with less labor, “which offers our clients the ability to lease, rent, or sell their building quicker, which can have large financial benefits that we don’t see on our side.”
According to two of mass timber’s most passionate and experienced advocates, Matt Tonello of Consigli Construction and Paul Becker of the architecture and engineering firm Thornton Tomasetti, the cost associated with some projects has been a factor of the immaturity of the industry. Mass timber has been common in Europe since the 1940s, but only made it to this country 10 years ago.
Tonello is an engineer and a project executive in the Portland office of Consigli Construction and has been leading the firm’s mass timber projects in New England for a decade.
Becker is a senior principal with the Portland office of Thornton Tomasetti structural engineers and architects, which has extensive experience with mass timber. Globally, the firm has designed over 100 mass timber projects, some just in concept, and three to four dozen projects in North America and Europe that were built in the past few years.
“There’s still a learning curve in the U.S.,” Becker says. “And that contributes to a cost differential that’s put on it for inexperience. The cost is less if the contractor has experience with the material and the process.”
He sees material costs offset by increased speed of production.
“Building with mass timber can often be quicker than a steel and concrete structure and is often lighter in weight, which has advantages including a reduced construction schedule, potentially smaller foundation costs, smaller cranes and a smaller crew to erect the structure,” Becker says. “You can put a home up with mass timber in three days.”
Thornton Tomasetti designed the tallest mass timber structure on the globe, the 25-story Ascent in Milwaukee, which will soon be eclipsed by the firm’s 375-foot Edison building, also in Milwaukee.
One of the firm’s current projects is the Roux Institute of Northeastern University, now under construction in Portland, which will use mass-timber in one wing of the six-story, 245,000-square-foot academic building. Construction is being managed by Consigli.
Tonello and Becker co-founded the Maine Mass Timber Advisory Council, which advises the University of Maine’s Mass Timber Commercialization Center, and serves as a research and development partner with the university’s Advanced Structures and Composites Center in Orono to innovate timber lamination and procurement processes, and with a goal of seeing mass timber manufacturing come to the state for the first time.
Fabricated panels and beams are custom-designed to fit each project. They’re delivered almost like a kit with holes for electrical components pre-drilled, and they go together more quickly — therefore less expensively — than construction with traditional materials.
And because the wood in mass timber builds is valued for the warmth it lends to buildings, it’s not usually covered with surface finishes such as paint, allowing for further cost savings.
Mass timber’s inherent ability to sequester carbon gives it another advantage. Becker explains that trees embody carbon whereas steel and concrete are energy intensive to produce and not sustainable.
The product’s low environmental impact has been a primary reason higher education institutions are bullish on it. Another factor is the phenomenon known as biophilia that supposes humans feel more relaxed in natural environments.
“Studies have shown that stress levels, cortisol levels, go down,” Becker says. “They’ve even found that in elementary school environments, the learning outcomes are better in a natural environment.”
Consigli has built or renovated 25 mass timber projects in New England and New York City. At Bowdoin College, Consigli recently built the John and Lile Gibbons Center for Arctic Studies and Barry Mills Hall, two buildings totaling 50,000 square feet, with concrete foundations but all mass timber above ground.
Consigli used mass timber for a wing in Boston’s Museum of Science and in facilities at Colby, Williams and Smith colleges, Harvard University, the University of Massachusetts at Amherst and at the University of Southern Maine in Portland, where the 40,000-square-foot Crewe Center for the Arts has just been completed.
Tonello is particularly excited about the firm’s 50,000-square-foot Green Engineering and Materials building under construction at the University of Maine’s Orono campus, which will be home to the Factory of the Future.
Despite its attributes and advocates, widespread adoption of mass timber in Maine faces two hurdles: there isn’t yet a manufacturing facility in New England, and while converts are multiplying, there isn’t yet enough demand to support the cost of a manufacturing facility, which is estimated to be hundreds of millions of dollars.
Wright-Ryan sourced the additional products it needed for the Katahdin project from New York-based Unalam, Nordic Structures in Montreal and from Mainely Trusses in Fairfield, a division of Hancock Lumber.
There are U.S. manufacturers — in Oregon, Montana, Arkansas, Texas, Wisconsin and Alabama — with different specialties and capabilities.
Becker favors products from Austria. “They are so good at it,” Becker says. “They make super high quality products with really high tolerances, so the components go together really well. And it’s more cost effective to ship it from Austria than truck it from U.S. sources.”
Tonello is developing a prototype for a lamination process using wooden nails instead of glue, which he envisions could be produced in Maine, perhaps using existing capabilities.
With the Portland Museum of Art project on the horizon, Bessire has been meeting with members of Maine’s forest industry to promote mass timber production. Bessire has said he would like to use Maine wood for the project.
“The dream is to have the wood sourced in Maine and have the grading and the milling, and to have plants here for CLT and glulam,” Bessire said at a mass-timber conference hosted by the museum last year. “We love Maine and we want to build a new industry that uses Maine resources to create jobs for the next generation. Maine is the most heavily forested state in the country.
“We need to figure out how to deal with these mill towns, how to make them lively and vibrant and to create excellent relationships between the rural and the urban.”
Thornton Tomasetti’s Becker says there are in fact several potential factory projects proposed for New England that are currently in the capital campaign phase, and he’s optimistic that production of mass timber in our region is on the horizon.
“It’s a process, but we’ll get there.”
0 Comments