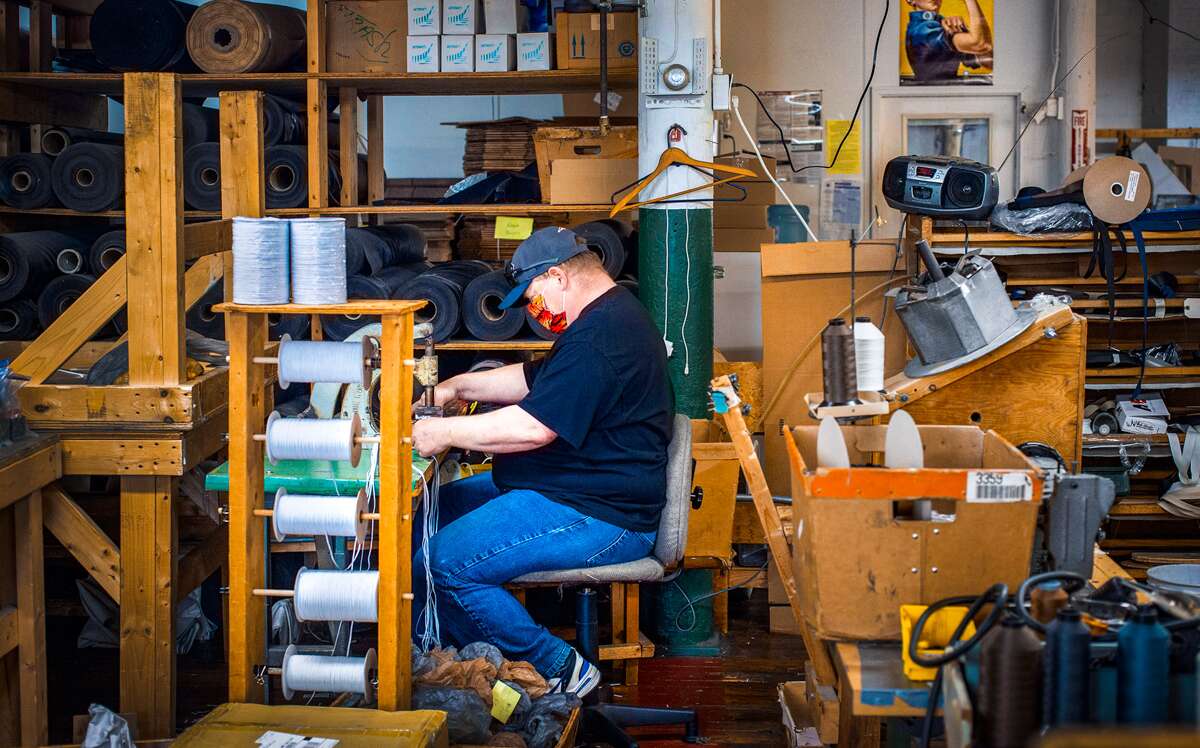
Please do not leave this page until complete. This can take a few moments.
In mid-March, Allen Manufacturing Inc. in Lewiston converted all of its production to make face shields and nonmedical cotton face masks.
Founded in 1975 as Fancy Stitchers, the company at its peak had 550 employees producing 86,000 leather handbags every week. In 2011, under its current owner David Allen, the company was renamed Allen Manufacturing and expanded to contract sewing, die cutting, light assembly and kitting. Output in the 15,000-square-foot facility is prodigious: Many large customers contract thousands of units, produced by a team of 12 employees.
Allen already had health care-related contracts for hospital bed parts and duffel bags for temporary hospital wall parts. He turned to face shields and face masks when he was contacted by the owners of Fabric Warehouse in Auburn.
“Tim and Chris Riley from Fabric Warehouse asked me if I could cut fabric for face mask kits,” Allen says. “They brought the material and we started cutting. At some point, they said, ‘Why don’t you make the face masks?’”
Since then, Allen has deployed his team to cut fabric and elastic bands for the masks, hired about 80 home stitchers and sold over 40,000 masks, almost at cost.
He’s also partnered with Fabric Warehouse to make face shields — clear plastic panels attached to headbands that provide full-face coverage. Fabric Warehouse supplies materials and Allen provides labor. Production is about 5,000 shields per week, with weekly capacity for 20,000. Those sell for a slight markup, says Allen.
“We didn’t start this to make money,” he says. “We started this to provide a service to the community and to keep my employees employed and to pay the light bill.”
Allen Manufacturing is one of numerous manufacturers, distilleries and breweries that, since March, turned from normal production runs to make healthcare products like hand sanitizer, aerosol boxes, face guards and non-medical face masks.
Much of the work is done in partnership with the University of Maine, which formed an “innovation team” to develop solutions to the shortages of supplies and challenges faced by Maine’s health care centers since the beginning of the pandemic (see sidebar).
The team includes the Maine Manufacturers Extension Partnership and Manufacturers Association of Maine, which sent out calls to members for help and maintain COVID-19 resource webpages that include companies producing resources, DIY mask-making instructions and more. (Links are on their home pages.)
“What we’re doing in Maine has completely blown me away,” says Lisa Martin, Manufacturers Association of Maine’s executive director. “Maine now has a substantial list of companies making PPE [personal protective equipment]. And it’s growing.”
Folks are eager to step up. After a newspaper article ran in late March on Allen Manufacturing’s efforts, David Allen was swamped with calls from home stitchers.
“That first day we got 80 phone calls,” he says. “Since then we’ve had 300 to 400 inquiries from people who want to make masks.”
At Thermoformed Plastics of New England in Biddeford, owner Paul Tyson recalls a day in late March. Maine CDC Director Nirav Shah had just given a press conference and talked about the need for face shields.
“A friend of mine called and said, ‘Are you making face shields?’” Tyson says. “I went online to see what a face shield was.”
After some research, Tyson realized he had the correct material — thin, clear, virgin polyester — to make 12,500 wrap-around plastic pieces. He shipped those to other companies to complete the assemblies, which were donated to medical facilities in Maine and New Hampshire.
Orders poured in. Tyson sourced 40,000 pounds of plastic to produce 600,000 pieces for the assemblies, which are sold at cost. By late April, he also expected to donate another 5,000 shields to nonprofits.
Typically, the company turns plastic into precisely finished products for the medical, food, retail, automotive and pharmaceutical industries. The shields meant clearing out other orders, with employees working overtime to free up machine capacity. He also asked nonmedical customers if they were willing to postpone their orders.
“They all said yes,” Tyson says.
In Gorham, Plas-Tech Inc. responded to Maine Manufacturing Extension Partnership’s call for help; its email listed PPE items in dire shortage.
“Two of the things we were able to easily assist with were disposable face shields and intubation boxes,” says Plas-Tech’s owner, Terry Webber.
The email included a link to an article about a Taiwanese doctor who had made an intubation box. The clear, three-sided box, with strategically placed holes, covers the patient’s head and shoulders to contain aerosol spray, allowing medical personnel to intubate safely. Plas-Tech made 264 for a Massachusetts company serving New England hospitals, 60 for Maine Medical Center, and single orders for hospitals around the country.
Similarly, he obtained dimensions from a sample face shield, ordered materials for 25,000, and bought equipment to cut and attach elastic straps.
“We designated an area of our facility to the production and moved a couple machines we used to this area, so we created a cell to process and assemble everything,” Webber explains. “We started working later hours each day along with Saturdays for the last month in order to work on normal customer work and these projects.”
When the pandemic started, Luke Davidson thought he might have to close his company, Maine Craft Distilling, which makes spirits and canned cocktails in Portland.
Then a doctor called, asking him to look into making hand sanitizer. Davidson had 1,000 gallons of high-quality alcohol in stock, originally intended for his normal springtime distillations. Instead, using a World Health Organization formula, he sourced glycerin and hydrogen peroxide and mixed everything for a batch of sanitizer, producing 4,000 quarts of hand sanitizer in a matter of weeks.
The process included making a charcoal column to filter impurities.
“It’s all hand-built by us with parts from NAPA and you name it,” he says. “It started pumping out gallons and we did it literally overnight. The team has been amazing.”
The team filled a pallet’s worth of vodka bottles, offered them at cost for $3 per bottle, and sold out quickly from the company’s storefront.
Customers picking up sanitizer often leave tips and charitable donations, which Davidson redirects to health care and other organizations. He’s donated sanitizer to the city of Portland and various organizations.
“Suddenly the flood gates opened,” he continues. “Requests started pouring in.”
When the vodka bottles ran out, Davidson called a friend at Oakhurst Dairy, which donated thousands of jugs. He ordered ketchup squeeze bottles for portable sanitizer. By late April, production was 8,000 gallons co-packaged for a larger facility in Massachusetts, plus 1,000 gallons sold from Maine Craft’s facility.
“Now we‘ve hired six new people and we’re nonstop 10 hours a day, seven days a week,” he says.
Other distilleries and breweries are partnering on production. “We got on the phone with the University of Maine,” says Jordan Milne, founder of gin-maker Hardshore Distilling Co. in Portland. “They said, ‘We need 400 gallons of sanitizer per day. We stopped short and said, ‘That is way more than we can produce on our own. We’ll have to get some help.’”
The first step was to source large amounts of alcohol. Milne contacted breweries that had ramped up keg production for events that never materialized.
“They were sitting on a bunch of inventory that was going to be poured down the drain,” he says. “We reached out and said, ‘Can we have that to distill?’ They said, ‘Absolutely.’”
Baxter Brewing Co. in Lewiston was one of the breweries. Kegged beer is best consumed within a certain period after production, explains Baxter’s president, Jenn Lever. Much of it would be dumped.
Instead, Baxter trucked 6,000 gallons to Sebago Lake Distillery, a small rum-maker in Gardiner, which performed an initial distillation. For beer that is 5% to 9% alcohol by volume, the initial distillation increases alcohol content to 30% to 40%, says Sebago Lake’s co-founder, Dan Davis.
Sebago Lake and other intermediary distillers send the results onward to Hardshore and others that have the right kind of still to attain 96% alcohol, required to make hospital-grade sanitizer. Hardshore delivers about 200 gallons of 96% alcohol per week to UMaine’s Process Development Center, which developed the mixing process, sourced glycerin and peroxide, coordinates the breweries and distilleries, and performs the final mixing, packing and distribution. So far, it’s produced 2,800 gallons.
Says Milne, “We’re talking about thousands upon thousands of gallons of Maine beer that’s turned into hand sanitizer.”
The projects have allowed companies to stay viable through the pandemic.
Normally employing four, Hardshore hired two additional employees to help with sanitizer production. Like other companies, Hardshore is balancing regular production, too.
“Production of gin went down because we made room for hand sanitizer production,” Milne says. “We almost missed a shipment of gin because we’ve been making sanitizer and that’s our first priority. But my team said, ‘If we distill all night tonight, we should be able to make gin tomorrow for that order.’”
Allen put all of his regular jobs on the back burner.
“There are lots of companies out there that have put their primary products aside and put their profits aside, as we have, and said, ‘I’m going to do what’s right for the country, regardless of impact on my company,’” he says. “That said, I haven’t heard any protests from my regular customers. They’ve said, ‘Yes, I understand. Let us know when you get back to regular production and we’ll start sending you orders again.’”
0 Comments