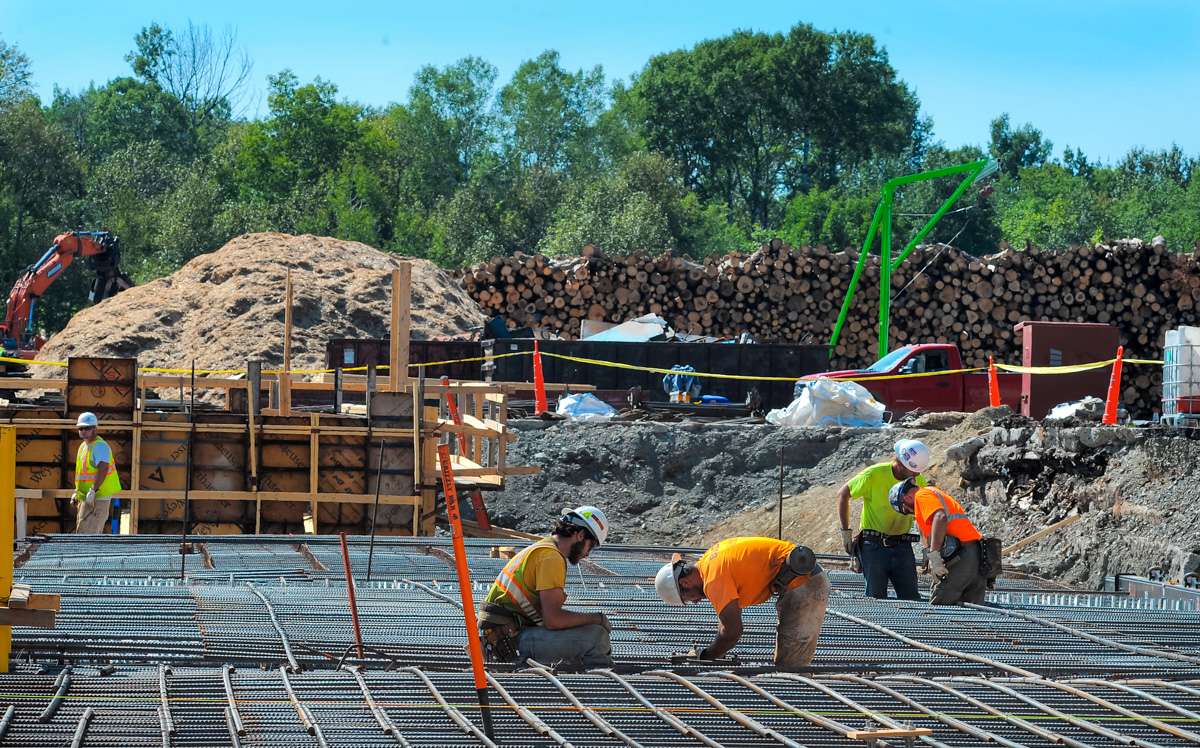
Please do not leave this page until complete. This can take a few moments.
As LP Houlton’s 160 employees keep busy this summer turning hundreds of thousands of tons of Northern Maine trees into millions of square feet of engineered–wood products, work was underway to expand the mill in response to increased demand for its flagship line, an exterior siding and trim called SmartSide.
“LP has seen consistent year-over-year growth of SmartSide and needed to add more capacity,” said Nathan Whitney, the plant’s manager. “With our location here, next to a plentiful wood basket, it made perfect sense to convert our mill.”
The $150 million expansion and conversion, which broke ground in June, is driven by market growth in the home construction, repair and remodel markets.
In turn, the investment “will ensure the mill continues providing hundreds of well-paying direct and indirect jobs across the region,” said Paul Towle, president and CEO of Aroostook Partnership.
LP Houlton, which is actually in the neighboring town of New Limerick, belongs to Louisiana-Pacific Corp. (NYSE: LPX), a manufacturer of engineered wood building products headquartered in Nashville, Tenn.
The mill is one of the largest employers in Aroostook County. Over the past year, it expanded its workforce and operating schedule as the home construction and remodeling market took off.
Those expansions and the construction that’s now underway are viewed as great news for Maine’s forest products industry, which in recent years has been hard hit by paper mill closures and the downsizing of the pulp and paper industry.
Loggers and communities in northern Maine are looking to move forward after “the toughest year they have experienced in living memory,” said Dana Doran, executive director of the Professional Logging Contractors of Maine.
“LP’s willingness to invest in the future of Maine’s forest economy and continue to provide a market for Maine wood is a hopeful sign for the logging industry,” Doran said.
This is LP Houlton’s second major expansion in recent history. As the parent corporation’s second-longest-running mill, it was commissioned in 1981 and has been producing “oriented strand board” since 1982.
In 2008, the mill added a “laminated strand lumber” line, which represented a $140 million investment at the time.
The two lines are used in the construction of the “innards” of a house, as Whitney said. Oriented strand boards are a type of engineered wood used primarily as wall sheathing, roof decks and subfloors in residential construction. Laminated strand lumber, developed to compete with traditional dimensional lumber, is primarily used as structural framing
With the latest investment, the mill is focusing on the building’s exterior with the exclusive production of the siding and trim line, which is one of the fastest-growing siding brands in the U.S., said Breeanna Straessle, LP’s director of corporate communications based in Nashville.
The investment and conversion is expected to increase LP Houlton’s consumption of local and sustainably sourced wood fiber by about 30%, which is expected to benefit providers across the supply chain, including local businesses.
“Aside from the logs, which will benefit landowners and truckers, we do a lot of business with local companies for supplies and repairs,” said Whitney. “For example, tires for our equipment come from local vendors. We use local companies that supply steel. Even the local market that sells pizza and subs benefits.”
Up to now, LP Houlton has been buying about 250,000 tons of primarily aspen logs per year. With the conversion, aspen consumption will increase to 350,000 tons, which will produce 220 million square feet of SmartSide. At full capacity, that’s enough siding for about 100,000 homes per year.
“We purchase 8-foot logs, primarily from within 60 miles of the mill in northern Maine,” said Whitney.
Some is also purchased from New Brunswick.
At the mill, the logs go into a pond to soften them up and make them easier to flake. The bark is then removed and the logs go through a big machine, appropriately called a flaker, that makes small flakes. The flakes are dried to correct moisture content, then layered in sheets with a topping of fine sawdust.
An additional paper overlay is impregnated with resin. The assembly then goes into a press, which has a specially made plate that’s textured to look like cedar siding. The assembly comes off the press as a sheet that’s further trimmed and finished.
Aspen, a hardwood, is considered ideal for the product due to its strength-to-weight ratio and its sustainability, said Whitney.
“Aspen will regenerate from its own roots,” he said. “And in Northern Maine, there’s not a lot of competition for aspen” due to the industry’s primary focus on softwoods such as spruce, fir and pine.
Aspen suppliers range from large corporate owners to small family-owned operations. Over 99% of the wood is utilized in the product, with the rest used for biofuel.
The conversion includes adding a 90,000-square-foot facility that will house new equipment to trim and finish the siding. Part of an existing building, where logs are received for debarking and conditioning, will be demolished and replaced.
The project’s general contractor is Miron Construction, headquartered in Neenah, Wis., which has worked with Louisiana-Pacific Corp. on similar conversions. Stantec, headquartered in Edmonton, Alberta, is providing engineering services.
The facility’s 16-foot-long press, built in 1981, is in the process of a rebuild that includes installation of new components such as controls and pressing plates. Other machinery will be added, including a new debarker, saws, paint booth, drying oven and packaging equipment.
LP Houlton will stop production in the fourth quarter of 2021 in order to finish site construction. It’s expected the facility will be back online as a SmartSide mill by the end of Q1 2022.
“We’ll do a lot of training while we’re down,” said Whitney. “Every employee will go through several rounds of training, especially around quality. This is an appearance product. It goes on the outside of a house and will be the first thing you’ll see as you go into someone’s driveway. We have to make sure there are no blemishes or bleed-through spots.”
As one of Aroostook County’s largest employers, LP Houlton increased its workforce substantially through 2020. A year ago, it employed just over 100 people working five days a week. Due to increased demand for home construction products, the plant went to 24/7 operations and now employs 160.
“We did quite a few rounds of hiring,” said Whitney.
Recruitment wasn’t difficult, he said.
“One of the biggest draws is that we’re an established company in the area,” he said. “We have very good pay and benefits.”
All of the employees, who range from recent high school graduates to veterans with 30-plus years of tenure, stayed through the past year.
“I’m proud to say they actually decided to come to work through the pandemic,” he said.
That said, it’s getting harder to find people, he added. Recruitment strategies include working with local schools, holding job fairs and advertising.
“Recently, we started offering a $500 sign-on bonus and a $2,000 retention bonus,” he said.
The conversion helps to solve for lost markets in other forest product sectors, said Doran. Maine’s timber harvesters and haulers were hit hard in 2020, when most logging contractors who are members of the association reported a 30% to 40% reduction in wood markets, he said.
Many are suffering severe revenue losses, layoffs, loss of clients, reduced productivity and inability to plan for the future, due to economic impacts of the pandemic and the loss of the Pixelle Specialty Solutions pulp mill in Jay to an explosion in April 2020.
“I look at any investment or expansion or new business startups as major news in our industry,” Doran said. “We want to make sure there are markets for every wood product in Maine. What LP is doing is an enormous benefit to the logging community.”
In Aroostook County, said Towle, “Farming and forestry are the primary drivers to our economy and we’re always encouraged when investments are made to sustain these industries through modern product manufacturing and value-added processing.”
0 Comments