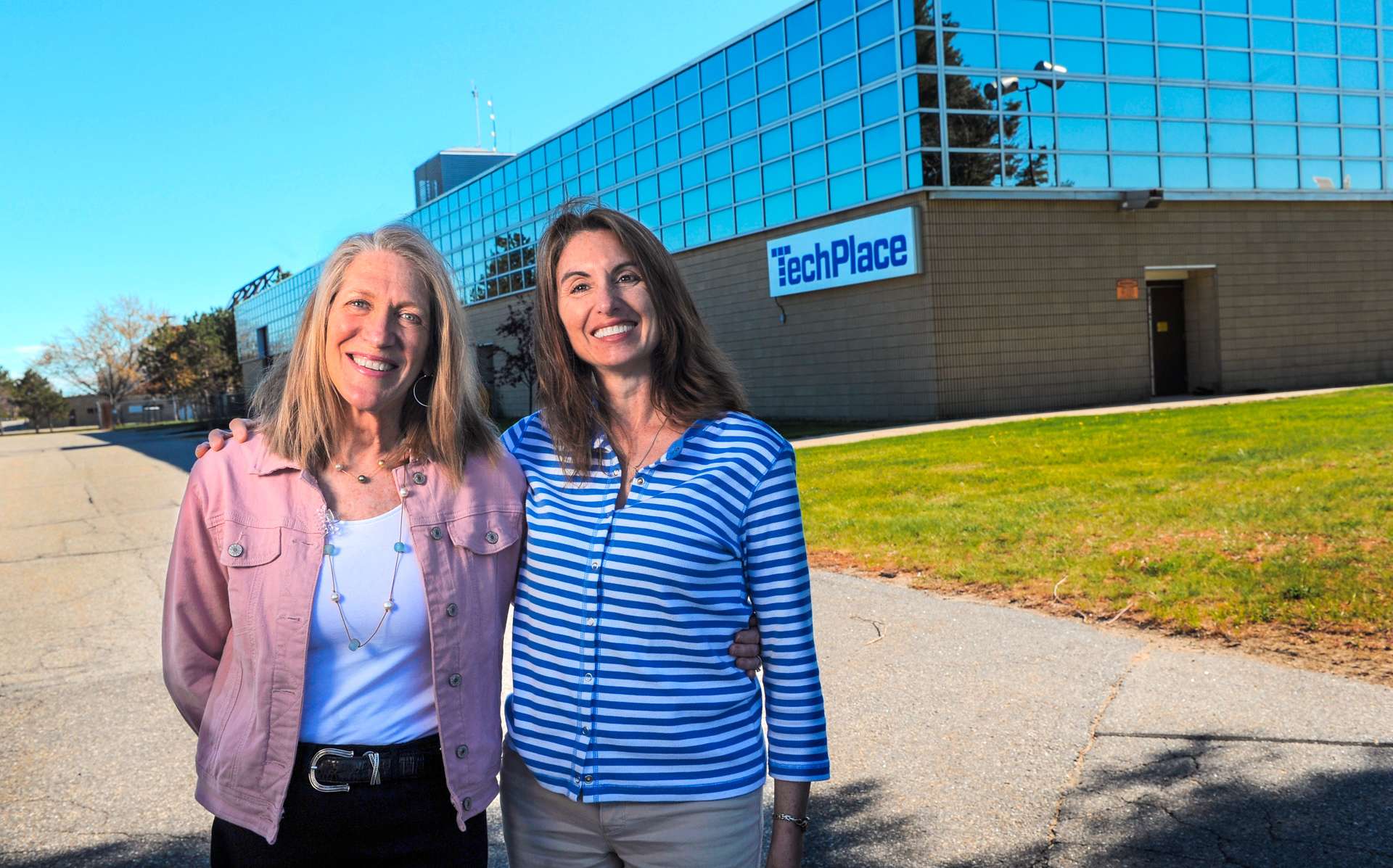
Please do not leave this page until complete. This can take a few moments.
Physical space is one of the biggest challenges for many startups. While many businesses start out in a garage, basement or spare room, at some point they need dedicated space. A maker of snacks needs a test kitchen to try out recipes. A kelp processor needs space for drying and processing. A packaging startup needs access to a CNC machine. A biotech company needs lab space. A rocket maker needs large areas for building prototypes and a dedicated area for launching.
As Briana Warner, CEO of Atlantic Sea Farms, says a move into bigger space is a major step — but often a necessary one as well. The startup recently moved into 27,000 square feet in Biddeford.
“[Our old space] was too small. We couldn’t fit the machinery in that we needed to grow. Our new space allows us to continue to grow and serve our customers and be adaptable,” she says.
With nearly every startup, at some point there’s a need to find physical space. That’s where a UMaine Innovation Center comes into play, or Tech Place at Brunswick Landing.
Here is a look at how some startups solved their space needs.
One of the best-known physical spaces is the University of Maine’s Foster Center for Innovation, a leading resource for innovation and commercialization, serving both the campus community and outside businesses and organizations.
The base for UMaine programs and services that support entrepreneurship, business development and commercialization of university research. The Foster Center provides courses, training, coaching and consulting to students, faculty and staff, startups and established organizations, helping them develop the skills needed to effectively create, test and actualize ideas.
The UMaine campus has been a hotbed of innovation when it comes to offshore wind power, and the Aqua Ventus project; the composite bridge system, called Bridge in a Backpack; and student-led projects like Ferda Farms, an oyster farming initiative.
Renee Kelly, an assistant vice president for innovation and economic development at UMaine, serves as a liaison to the state’s economic development community and identifies opportunities for UMaine to partner with organizations to improve Maine’s economy. She also leads the Foster Center, as well as the Maine Innovation Research and Technology Accelerator program, UMaine’s I-Corps Site and business incubation programs.
On Brunswick Landing, a former Navy base with an abundance of cavernous buildings, an air strip, aircraft hangars and developable land, TechPlace was a natural place to take root.
TechPlace offers affordable space for offices, light industrial use and clean labs.
At present it has 38 tenants, or “members,” as it calls them. The members are in spaces that ran from 200 square feet to 3,000 square feet. Some startups there have both office space and industrial space.
“We’re 98% full,” says TechPlace director Jaimie Logan.
On a recent tour, Logan introduced me to the site’s longest-tenured tenant, Daniel Greisen of Greisen Aerospace, which on a recent day was creating a jig that the Air Force could use to make missile parts.
Other tenants with large-scale operations include Nathan Varney, whose VarneyCNC was making composite parts for clients Bath Iron Works and its arch-competitor, Huntington Ingalls Industries, which is based in Newport News, Va.
Other businesses at TechPlace run the gamut.
Cem Giray is CEO and president of Salmonics, a lab that produces reagents and products such as fibronectin and serums from the unused blood of farmed salmon.
Melissa LaCasse, who is an entrepreneur program at the Roux Institute, is developing sustainably produced packaging materials that can be used in place of plastic and styrofoam packaging. Her company, Tanbark Molded Fiber Products, uses TechPlace for storage, with production being tackled in Saco.
Running Tide, which is based in Portland and is oyster farming and kelp-raising operations. On a recent day at TechPlace, Josh Hardy of Running Tide was outfitting a shipping container for kelp processing; the container was being readied to go to Iceland. Separately, the team was building a large galvanized steel system for oyster-farming.
Jack Quinn, who retired from IDEXX Laboratories and now leads Hound Bio, is doing research related to pet medicines.
Clamar Floats produces the pontoons used on float planes. The process looks much like boatbuilding, with large-scale molds and a lot of fiberglass. The floats are shipped all over the world, but many go to Alaska.
Unlike some of the more industrial parts of TechPlace, Cassandra O’Brien and Megan Hall work in a clean lab. They work for Loam Bio, which creates products that remove CO2, allowing agricultural uses to have less of an environmental impact. Loam Bio is an Australian company whose U.S. headquarters is in Minneapolis.
Ocean Renewable Power Co. produces equipment to harness tidal currents. The firm has a statewide presence. It is headquartered in Portland. It does energy testing in Eastport. It teamed up with Millinocket Fabrication & Machine to manufacture the turbine shafts for its portfolio of products. And its electronics and engineering lab is at TechPlace.
BluShift Aerospace’s first dedicated space was a former Navy garage on Brunswick Landing. It was cramped, poorly lit and drafty.
“At the time we didn’t need much more than a garage. But it was rudimentary. There was no insulation. We were bundled up. You had to take your gloves off to get anything done,” says Sascha Deri, bluShift’s founder and CEO.
At the time, many of the tools the company needed were basic — “95% of them you’d have in the garage at home.”
It was hard to beat the rent, which was $300 a month.
For larger needs, such as a CNC machine or an industrial-sized lathe, bluShift paid for time at nearby TechPlace, also on Brunswick Landing. For certain projects, bluShift was even able to hire out welders, who were moonlighting from another company.
As the startup grew, it needed larger dedicated space, which led it to its current site, at 2 Pegasus St. at Brunswick Landing, an aircraft hangar with a large, heated workshop and office space.
“As we’ve grown our engines have grown,” Deri says.
Deri says Maine could still benefit by having a large-scale 3D metal printer, an item that could cost $500,000 to $1 million. But an even more pressing need for bluShift is a place to launch the rockets.
Jonesport shot down his proposal to launch rockets there. He’s in talks with Steuben, on the Downeast coast, and sent out a request for information with the idea that towns that are open to the aerospace industry might reach out.
Ryan Beaumont is a University of Maine-trained engineer and inventor who has designed and built a range of engineering marvels.
But when it comes to workspace, he’s been able to set up shop in a wide range of places, often dictated by the physical size of the products he’s engineering.
He’s developed large-scale mechanical systems, like production machinery for a paper mill and electrical-and-control systems for a tidal energy project. He’s also been the principal investigator for the R&D and tech transfer for a walking bike and recreation aid for people with balance impairment.
In short, he’s worked on large-scale systems and smaller products — all of which have had different space needs. As a result, Beaumont has adapted a flexible approach to his workspace needs.
In college, he had access to UMaine’s Foster Innovation Center, which is outfitted with everything from advanced computer programs and CNC machines to workbench space and basic tools.
But in recent years, his work is where the workbench is.
“I was in Fort Andross in Brunswick. They have units with carpenters, musicians and restaurants. There’s always space available,” he says. “What I really needed was space to lay these things out. I needed rack space, bench space, space to layout and do shipping and receiving.”
He then worked out of Tech Place on Brunswick Landing.
“That was the right spot for me at the time,” he says, adding that he started working with a manufacturing partner, eliminating the need for larger space.
The manufacturing partner, Alexander’s Mechanical Solutions in Bangor, is a full-service job shop, doing everything from machining to welding.
With manufacturing being done at a different site, Beaumont, who owns the startup R.M. Beaumont Corp., moved operations back to his Topsham home, outfitting his garage as a workspace for smaller prototypes.
“The journey took me back to the garage,” he says.
Maine Crisp Co. is, with help from Sheridan Construction, in the process of fitting out 17,500 square feet of dedicated space in Winslow. It’s a $2.4 million fit-out.
The company, which produces gluten free chips and was founded by Karen Getz in 2014, has recently been in 1,500-square-feet at Railroad Square in Waterville.
But for a number of years Getz was producing Maine Crisp products from her home kitchen — which created some interesting challenges, as she relates.
“To start, I had to get the kitchen inspected and certified. As a gluten-free product, we no longer allowed anyone to bring gluten products into our home. As the company grew, I took over most of the kitchen with my ingredients, sheet pans, mixer, slicer and convection oven. It was a constant battle to keep humidity levels down for the crisps,” she says.
“We have a back sunroom that stored all of the packaging and cardboard plus a table for packaging crisps. The foyer became the storage area for bulk ordering of ingredients and UPS would pick up daily from the front porch. Oh and an office upstairs!”
Even the move into Railroad Square represented a big upgrade. “I baked from home for two years until the Railroad Square space opened up. It was great at first, I barely made a dent in the amount of space, which is about 1,500 square feet. Now we rent additional space down the hall and turned a large room into a cooler room for ingredients. The new space in Winslow is looking great at 17,500 square feet and we expect to move in late July or early August.”
0 Comments