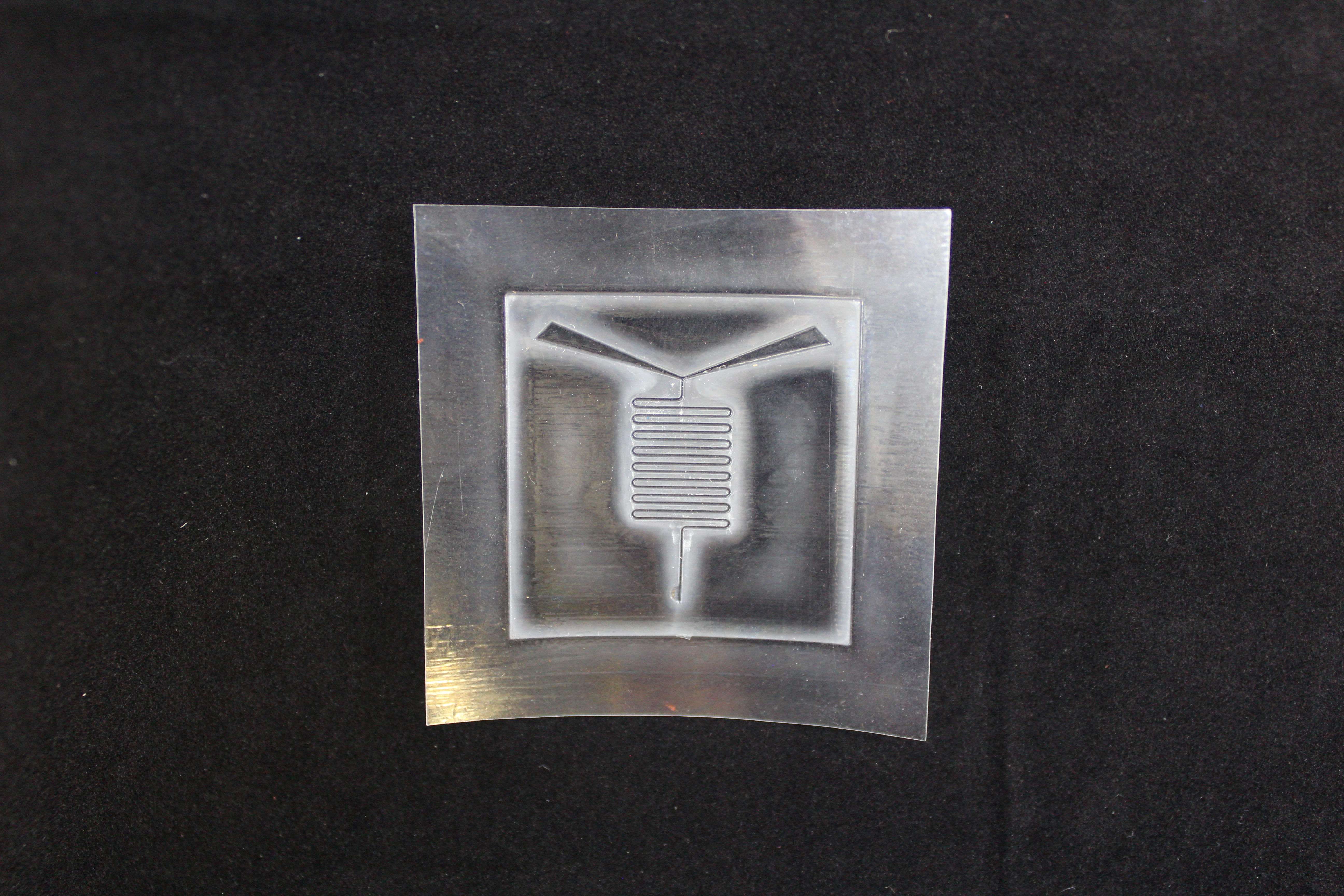
Please do not leave this page until complete. This can take a few moments.
Technology that’s typically used to make patterned paper for the fashion industry could also be a used to mass-produce water purification systems and medical devices.
Caitlin Howell, an assistant professor of biomedical engineering at the University of Maine, has been working with Sappi North America in Westbrook to explore the use of the company's "patterned-release" paper for use in biotechnological applications.
The use of papermaking equipment could be a way to produce biotechnology devices at high volume and low cost, according to a news release.
Howell is leading an initiative that also includes researchers at Harvard University’s Wyss Institute for Biologically Inspired Engineering.
The Harvard group invented an off-grid, portable water purification apparatus, called AquaPulse, that uses a pulsed electric field to kill bacteria, parasites and viruses. The system uses a series of tiny "microfluidic" channels to expose the water to the electric field, eliminating the need for filters.
The AquaPulse is intended to provide fresh water to millions of people who currently rely on contaminated water sources, according to Harvard.
Existing solutions use filters that require regular replacement and can easily become clogged, making it too expensive for many communities.
However, making the AquaPulse devices widely available at a low cost requires a method to mass-manufacture the microfluidic channel system.
So Howell approached Sappi about repurposing the company’s nanoscale texturing capability, which is part of its Ultracast paper manufacturing process, for fast prototyping of the microfluidic systems that go into the AquaPulse system.
The National Science Foundation recently awarded the project $154,566 in Established Program to Stimulate Competitive Research Infrastructure Improvement funding.
“Microfluidic” refers to systems that process small amounts of fluids using tiny channels, according to sciencedirect.com.
Microfluidic devices have potential for uses that require precise control of fluids, Howell told Mainebiz.
Howell said she got the idea for tapping Sappi when she was at a conference with some of its employees and learned about the precise patterning the company could do on a large scale.
The process applies to a type of product that Sappi makes, called “patterned release paper,” said Nicholas Yardy, Sappi’s director of release technology.
The process starts with a roll of paper made from wood fibers chosen for their high strength. A liquid coating is applied to the paper. The coated paper passes around an engraved cylinder in a continuous rotary process. The coating forms to the engraving on the cylinder and is further cured so that it comes off as a durable solid coating.
The resulting patterned release paper forms a type of shallow-relief mold that’s primarily used in the textile design world, said Yardy.
“When we talk about ‘release,’ the object you’re creating is manufactured in contact with our paper and then removed, or released, from that paper,” he said.
The paper is used to impart texture to textiles such as synthetic boot leather and vinyl seating.
Sappi ships rolls of the textured paper to customers worldwide.
“Customer X then applies a liquid plastic onto the paper, then laminates in a textile, dries it, vitrifies it, and releases the now-solid plastic from the release paper,” he continued. “Now you have polyurethane plastic backed by a textile that looks like the paper. That fabric then goes off to become shoes, handbags and car upholstery.”
The release paper can be reused. One square meter of release paper can make 20 or 30 square meters of synthetic leather.
“Some of the biggest brands in the world are customers of ours,” he said.
Enter Howell.
Talking with the folks from Sappi, “We said, ‘Let’s make patterns not for textiles, but for microfluidic channels,” she said. “We figured out a way to do that easily and quickly.”
The patterns for mass producing microfluidic devices had to be precise and repeatable but also easy to modify and refine. Howell used a 3D printer to create multiple small stamps imprinted with the inverse pattern of the device in question — similar to the stamps that come with a child’s Play-Doh kit. The stamps are lined up in Sappi’s casting machine. The dimensions of the channels in Howell’s initial devices were 400 microns wide — about the width of four hairs.
“We can go from 3D printed concept design immediately to this roll process,” Howell said. “We’re trying to make it so that people can have ideas about patterns and test them quickly and cheaply.”
Soon, Howell realized the potential for the new process for the work being done at the Wyss Institute, where she was a postdoc and technology development fellow from 2012 to 2015 and focused on developing and translating bio-inspired technology to market.
There, work was underway on the AquaPulse. But the problem was figuring out how to manufacture the devices inexpensively.
“We said, 'Maybe this concept we’ve developed would work,’” Howell said. “We now have a system where we can try a bunch of channel geometries and manufacture them in a way that would work best.”
The process also has potential for diagnostic devices such as blood tests, she added.
So far, Sappi has produced hundreds of patterns on numerous pilot rolls, testing factors such as microfluidic configurations, surface treatments and materials.
“The great parity between Caitlin’s work and our capabilities is that we’re set up to mass replicate textures,” said Yardy. “She has need of thousands of copies of her device and Sappi is specifically set up for the mass replication of textures with remarkable precision.”
The collaboration will continue.
“Caitlin been a strong supporter of our business as we’ve explored novel ideas,” said Yardy. “Her connection into the functional texture world is particularly of interest to us.”
Sappi announced last week that it has extended its current SmartWay Transport Partnership, an innovative collaboration with the U.S. Environmental Protection Agency. The SmartWay Transport Partnership provides a framework to assess the environmental and energy efficiency of goods movement supply chains and benchmark overall performance.
This is Sappi's 12th consecutive year as a SmartWay Transport Partner, and the company will continue to contribute to the partnership's savings of 279.7 million barrels of oil, $37.5 billion in fuel costs and 134 million tons of air pollutants. The collective effort is the equivalent of the annual electricity use in 18.2 million homes.
The Giving Guide helps nonprofits have the opportunity to showcase and differentiate their organizations so that businesses better understand how they can contribute to a nonprofit’s mission and work.
Learn MoreWork for ME is a workforce development tool to help Maine’s employers target Maine’s emerging workforce. Work for ME highlights each industry, its impact on Maine’s economy, the jobs available to entry-level workers, the training and education needed to get a career started.
Learn MoreWhether you’re a developer, financer, architect, or industry enthusiast, Groundbreaking Maine is crafted to be your go-to source for valuable insights in Maine’s real estate and construction community.
Learn moreThe Giving Guide helps nonprofits have the opportunity to showcase and differentiate their organizations so that businesses better understand how they can contribute to a nonprofit’s mission and work.
Work for ME is a workforce development tool to help Maine’s employers target Maine’s emerging workforce. Work for ME highlights each industry, its impact on Maine’s economy, the jobs available to entry-level workers, the training and education needed to get a career started.
Whether you’re a developer, financer, architect, or industry enthusiast, Groundbreaking Maine is crafted to be your go-to source for valuable insights in Maine’s real estate and construction community.
In order to use this feature, we need some information from you. You can also login or register for a free account.
By clicking submit you are agreeing to our cookie usage and Privacy Policy
Already have an account? Login
Already have an account? Login
Want to create an account? Register
In order to use this feature, we need some information from you. You can also login or register for a free account.
By clicking submit you are agreeing to our cookie usage and Privacy Policy
Already have an account? Login
Already have an account? Login
Want to create an account? Register
This website uses cookies to ensure you get the best experience on our website. Our privacy policy
To ensure the best experience on our website, articles cannot be read without allowing cookies. Please allow cookies to continue reading. Our privacy policy
0 Comments