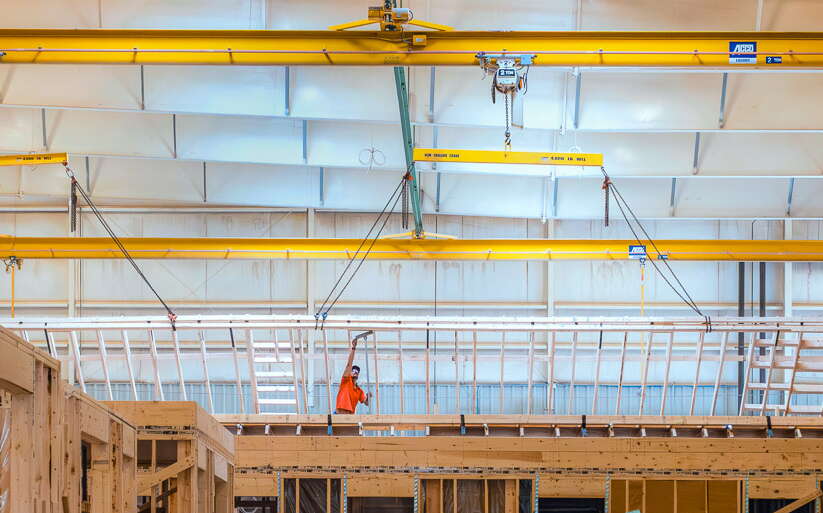
Please do not leave this page until complete. This can take a few moments.
Modular and panelized construction is trending up for residential and commercial builds. We talked with three companies seeing increased demand for their products and services.
Factory prefab can provide greater certainty around construction timelines and replicable design details and efficiencies.
It can make it easier to train employees and to retain older workers. For employees who no longer have to commute long distances to build on-site, there’s something to be said for a better work-life balance.
But there are also new skills to learn when it comes to assembling the components once they reach the construction site.
“We can build in our factory just about anything you can build in the field,” says Thatcher Butcher, president of KBS Builders.
KBS designs and manufactures modular structures for residential, commercial, and mixed-use buildings, working with developers, general contractors, architects, and builders to customize and produce the exact type of modular structure they’re seeking.
The company’s factory, in South Paris, spans 100,000 square feet and employs nearly 130 people.
“Our goal is to bring industrialized construction technologies to builders and developers traditionally stuck in the site-build world,” Butcher says.
Founded in the early 2000s, KBS is a subsidiary of Old Greenwich, Conn.-based Star Equity Holdings Inc. (Nasdaq: STRR; STRRP), with a building solutions division.
Butcher’s career spans the construction industry supply chain. He came to KBS four years ago to grow and modernize the business.
In the second half of the 20th century, Maine was a hub of off-site modular and manufactured housing companies, he says.
“We’re working to revitalize the industry,” Butcher says. “It’s needed from the jobs perspective, but, more importantly, because of the need for more housing.”
Contracts in Maine over the past year include scores of affordable housing units across developments in Newcastle, Madison and Boothbay; a condominium development for Rumford’s Black Mountain ski resort; stand-alone homes in Thomaston; 40 modules for townhouse condominiums in Lincoln County; 32 modules for mixed-income housing units in Portland; and 28 modules for townhouses in Bowdoinham. KBS builds additional modules for developments beyond Maine.
The company takes one or two big projects per quarter and infills that with smaller residential modules.
Once the units are built in the factory, they’re shipped to the site, assembled and connected to utilities.
Although the process doesn’t save on upfront costs — labor and materials are just as pricey off-site as on-site — it can save on carrying costs. An apartment building can be ready in months, versus years, lowering development costs and generating rents sooner.
“The upfront costs might be a little less, but it’s not as compelling,” says Butcher. “What’s compelling is being able to inhabit that building in a fraction of the time.”
The process addresses workforce shortages in a couple of ways. Factory construction brings in work aids such as cranes, jigs, and worktables, with construction performed at ground level — better for safety and less physically taxing, allowing employees to work later in life.
“You’re not hand-carrying stuff like shingles up to the roof with a ladder,” says Butcher. “We routinely have people continuing to work right up until they retire, versus having to find less physically taxing work by their late 40s.”
Another benefit? A higher production rate.
“We’re usually able to produce four to five times the amount of square footage per person per year, versus on-site construction, because it’s much more efficient,” he says.
Some of that is due to the elimination of long, daily commutes to on-site projects in remote rural areas.
“They wake up at 3 a.m., get to the job site at 7 a.m., take advantage of good weather days, work longer days, then leave at 7 p.m. and get home at 11 at night,” he says. “Most of our workers live within half an hour of our facility. They can put their kids on the bus, make those baseball games, and have a much better work-life balance.”
Then there’s construction efficiency.
In the field, “The framer does his work. He leaves. The house sits there a week. Then the roofer shows up. A week or two passes. Then the sider shows up,” says Butcher. “We have all those workers in the factory back-to-back. The moment one crew is finished, the work moves on. We eliminate those delays and wasted travel times.”
Backyard ADUs, headquartered at 247 Coons Road in Brunswick with teams in Maine and Massachusetts, was founded in late 2019 by Christopher Lee and Austin Gregory to design and assemble net-zero-ready modular homes as accessory dwelling units, accessory apartments or granny flats, combining prefab construction techniques with on-site construction.
The mission grew to include houses and apartment buildings. Backyard now has 36 employees.
“We’re building one house per week, to be two houses per week by the end of 2025,” says Lee.
Backyard facilitates the planning process, works with off-site construction partners to build components, and provides sitework, assembly and finish.
“We cut our teeth over the last five years figuring out how to design, price and build a modular structure predictably and affordably,” he says.
The builds go quickly.
“When all the parties are coordinated, it cuts the time by 30% to 40% overall” compared with on-site construction, he says. “It’s pretty significant. From groundbreaking to move-in, in a single-family house, it only takes us eight weeks and we’ll compress that to six weeks going into next year. It’s extremely fast.”
There are also pre-construction gains. Lee says his company can design iterations and pricing updates at the same time, smoothing the way to final drawings in perhaps three months versus eight to 12 months.
Lee notes that, while employee training might be easier on the factory side, on-site assembly requires an understanding of a process that differs from conventional builds.
“It’s extremely different from a typical job site,” he says. “So it’s been difficult for us to hire and train and get people into a mindset where, every day that passes after you put the box on the foundation actually matters with the overall schedule.”
A key difference? The modular units hit the foundation complete with drywall, plumbing, electrical and finish. That leaves a punch list of tasks that need to be completed in a precise order.
“It becomes a detailed project management problem,” says Lee. “If you mess up the order of operations, you can all of a sudden be ripping out drywall and reworking things and losing a lot of the efficiency that was gained in the factory in the first place. It’s a different skill set.”
Backyard obtains most of its modular volume from Professional Building Systems in Middleburg, Pa. KBS, also a supplier, is working with Backyard on the development of 20 energy-efficient, affordable condos at Maine Cooperative Development Partners’ Dougherty Commons in Portland.
“The big thing we do, that’s made modular work well, is that we’re very specific on utility hook-up details and the finish details when the boxes hit the foundation,” says Lee. “That’s typically one of the gaps when people leave it to figure out in the field. We’ve learned we’ve got to figure it out up front, with long, detailed conversations between the factory engineers and our engineers.”
Ryan MacEachern started his modular career with KBS and set off on his own in January 2020. His company, Maker Construction in Hebron, has five employees and two primary lines of work. He manufactures panelized components such as walls and roofs for other builders. And he performs sitework and assembles buildings made from panels and modules built by his own team or by other manufacturers.
His primary partnership is with BrightBuilt Home, a Portland firm offering architectural design and project facilitation for high-performance and modular residential design.
The two firms worked with Zero Energy Homes, a Mount Desert startup, on the design and production of wall, floor and roof panels for a single-family demonstration home in Searsport to show that modular construction combined with “net zero energy” principles can be priced for the affordable housing market.
Maker provided full wall panels with pre-installed windows and exterior house wrap, along with roof and floor panels. The shell structure was assembled in one day and is completely weather-tight, says MacEachern.
MacEachern plans to grow the “panelization” portion of the business for residential development.
Advantages of panels, he says, include being able to build the components off-site, flat-pack and ship them.
“The name of the game is not to produce the cheapest home,” he says. “Everything is higher-end and net zero energy. The wall systems are robust.”
Modular construction is essentially large box portions of a building with the interior dry wall and finish completed. The system uses smaller sections of walls, floors and roofs that need to be assembled and has less finish work done.
“They both have their place,” says MacEachern. “Generally speaking, the product can be manufactured while the foundation is going in, as opposed to waiting until the foundation goes in and then bringing the raw material to the site and starting to assemble it.
“That’s the main gain — it can be manufactured while the earthwork is being done. The foundation’s done and then bam, the product shows up.”
A modular home build, he estimates, can be assembled and finished in a matter of weeks.
“If you stick-built it, you can’t even consider that,” he says.
There’s considerable efficiency, too.
“You have an assembly line, the tooling is setup, the employees do specific processes,” says MacEachern. “Just by the nature of it being a manufacturing facility, it’s going to be faster.”
“A big part of the time and the hang-up with site-built is — you do, say, the rough framing and the sheathing but the electrician and the plumber aren’t necessarily going to be there the day after the framing is done,” says MacEachern. “It’s worse now than in the past because of the lack of tradespeople and everyone is so busy.”
Off-site manufacturing is more cost-effective and a better way to build, he says.
“Your materials are stored inside and all the work is being done inside, under cover,” he says. “You’re not out in the elements all year long. You’re probably moving a little faster.”
More off-site manufacturing is needed, says MacEachern. “It can’t not trend that way, with all of the issues we have going on — the need for housing, the shortage of available labor, the lack of knowledge in the trades,” he says. “It lends itself to all of that. And generally speaking, it makes more sense. There’s a misconception with off-site construction that it’s lower quality, cheaper built. But it’s not. A lot of modular houses we do are very high-end.”
He adds, “Off-site production can be a substantial means to solving the affordable housing crunch. You can’t get to that level of home construction in Maine without engaging the off-site manufacturing end of the business.”
0 Comments