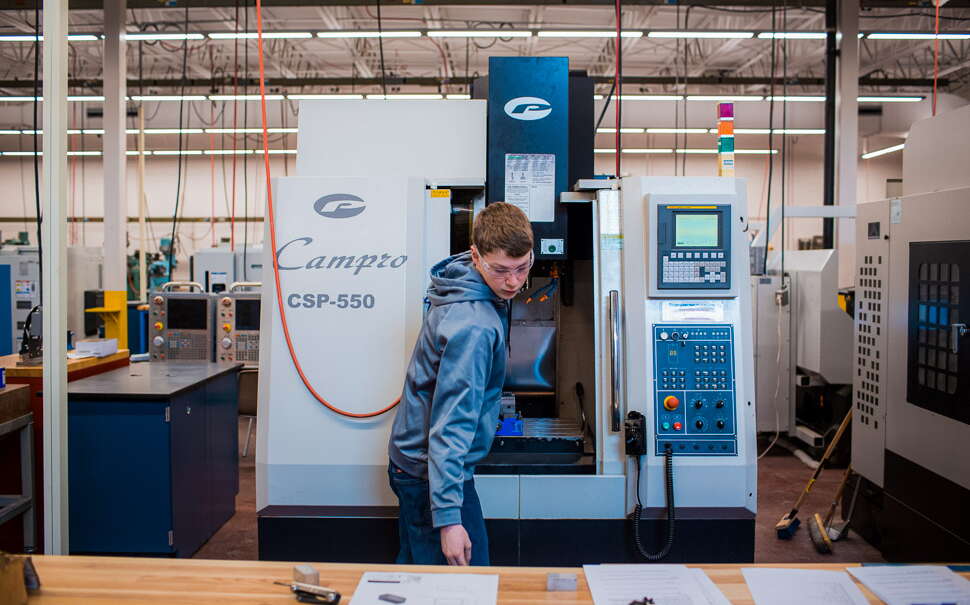
Please do not leave this page until complete. This can take a few moments.
A large “Now hiring” banner hung outside the Nichols Portland manufacturing plant on a heavily traveled road near the Portland-Westbrook line for weeks on end this past winter.
The sign was a small, yet telling, indicator of what manufacturing facilities all over Maine are facing. With an employee base that is aging out of the workforce, manufacturers are going all out to hire and train new workers to take their place.
Nichols Portland, which manufactures components for fuel, oil and hydraulic pumps, will hire and train anybody with the right attitude and desire who walks through the door. The company last year hired an extra human resources employee so staff could make more connections with Career and Technical Education (CTE) programs, high schools and community colleges to raise awareness about what they do and the employment opportunities they offer.
Students, teachers and school administrators are touring the plant in large numbers so Nichols Portland can show them “here we are, here’s what we do,” said general manager Frank Walton.
On this particular day, Walton has signed two more retirement forms from employees who are ready to hang it up after years on the job. They’ve put in their time and ready to retire, an increasingly common occurrence that’s being played out across Maine.
“If I had 20 of the right people walk in the door today, I would hire them,” Walton said. “We’re going to hire you for fit and train you for skill. We’ve got lots of opportunities.”
John Lewis, a managing partner of Synergy Workforce Solutions workforce development consulting firm, said there are plenty of training opportunities for people to learn welding, machinist and other technical skills that are in demand. But the trick nowadays is to make people aware of the jobs that are coming open in those fields as people retire.
Like Nichols Portland, other manufacturers are forging partnerships with CTEs, high schools and others to build brand awareness and make students mindful of the opportunities. There’s been a lot of talk in recent years about the “skills gap” — where the skills of incoming employees don’t match the skills required for the job — but Lewis thinks an “awareness gap” precedes the skills gap.
Lewis, who serves on the Manufacturers Association of Maine’s workforce development committee, said it’s important for manufacturers to get in front of students to drive home what they do. He knows of a boatbuilder, a construction company, a dairy and other types of businesses that are strategically forging partnerships with schools to build awareness among the workforce of the future.
“How do you connect what they’re doing in the classroom to what you’re doing in the real world,” he said. “It raises that awareness but also gives students that sense of, ‘Oh, there is a reason why I’m learning this.’ It’s important and teachers appreciate that. You’re coming in and reinforcing what educators are doing but also turning on some lightbulbs at the same time.”
With nearly 1,900 manufacturing businesses that employ about 58,000 workers, manufacturing is Maine’s fourth-largest industry, generating over $6.3 billion each year, according to the Manufacturers Association of Maine. The companies make paper, metal, textiles, boats, electronics, food and beverage products, medical devices, military and aerospace products, and more.
The Maine Department of Labor’s latest Job Outlook for Maine report says a combination of a declining birth rates and thousands of baby boomers retiring has raised concerns that there won’t be enough people to fill the workforce demand in the years ahead.
In 2022, the largest share of Maine’s population was 55 to 64 years old. An average of 68% of this group typically is in the labor force. In 2032, that group will be 65 to 74. An average of 25% of this age group usually are in the labor force; most are retired.
The report projects that the overall number of employees in manufacturing will fall slightly through 2032. However, because workers are older — Maine is the nation’s oldest state — there will be hundreds of manufacturing jobs that come open each year because people are retiring. That exodus is resulting in openings in production, maintenance, engineering, and other jobs, and a need to train new workers or upgrade skills of current workers.
Among those offering training is the Maine Community College System. Bolstered by grants totaling more than $90 million from the Harold Alfond Foundation, MCCS has provided short-term workforce training to tens of thousands of Mainers in many fields in recent years. The training programs are offered onsite at Maine’s community colleges, at workplaces, online and through third-party instruction.
The foundation’s most recent grant is for training programs aimed at three focus areas: manufacturing, construction and healthcare. Since 2021, the system has provided training for 131 manufacturers for both new hires and for incumbent workers who are upgrading their skills, said Dan Belyea, chief workforce development officer for the Maine Community College System.
“Their workforce is aging out and they need those folks to replace them,” he said.
Furthermore, manufacturers are realizing that with large numbers of employees embarking on retirement, there’s a need to tap into their institutional knowledge before they leave the workforce, said Jim Fay, president of the Maine Manufacturing Extension Partnership. That “knowledge transfer” involves both technical skills — such as operating equipment, quality management, workplace safety and the like — and behavioral skills such as leadership, collaboration and team-building.
“What they’re recognizing is that they have people who have been around for decades, who have worked well together, and the ‘secret sauce’ is kind of walking out the door,” Fay said. “So, what can do they do to recreate a different ‘secret sauce’ with the new workforce, recognizing there are different ways to do that, both with technical training and behavioral or soft skills training.”
While most manufacturers are small and medium-sized, even the largest are focusing on the need for more skilled workers in the years ahead. Navy shipbuilder General Dynamics Bath Iron Works, which has 6,800 employees, has extensive training programs for people before they’re even hired on through their careers at BIW.
“We build complex, sophisticated ships that require thousands of highly skilled employees to bring them to life, so workforce training is extremely important at BIW,” said Ray Steen, a VP. “We are investing heavily in all levels of training and many different types of training: pre-hire training, skills-based training, on-the-job training, classroom training, leadership training and professional development.”
Like many manufacturers, BIW has also gotten creative in seeking out future employees. It has a tractor-trailer that travels to schools and events around Maine and beyond to expose young people and other prospective employees to shipbuilding. The trailer has visited vocational schools in central and eastern Maine as well the Fryeburg Fair, Laconia Motorcycle Week in New Hampshire, the Moxie Festival and the Maine Sportsman’s Show.
BIW also has a new partnership with JMG (formerly Jobs for Maine Graduates) where a BIW staff person travels to different CTE schools to promote shipbuilding and make sure they have training available that would make them good candidates for shipbuilding careers.
Beyond training and finding new ways to reach the workers of tomorrow, some companies are also looking at things like automation, robots and artificial intelligence as ways to reduce their workforce needs. For example, Fay said, companies can use collaborative robots to perform repetitive jobs that are often hard to fill, like loading things on pallets or in boxes.
“If you don’t have people,” he said, “one of the options is to look at how to automate some of the more redundant tasks.”
0 Comments