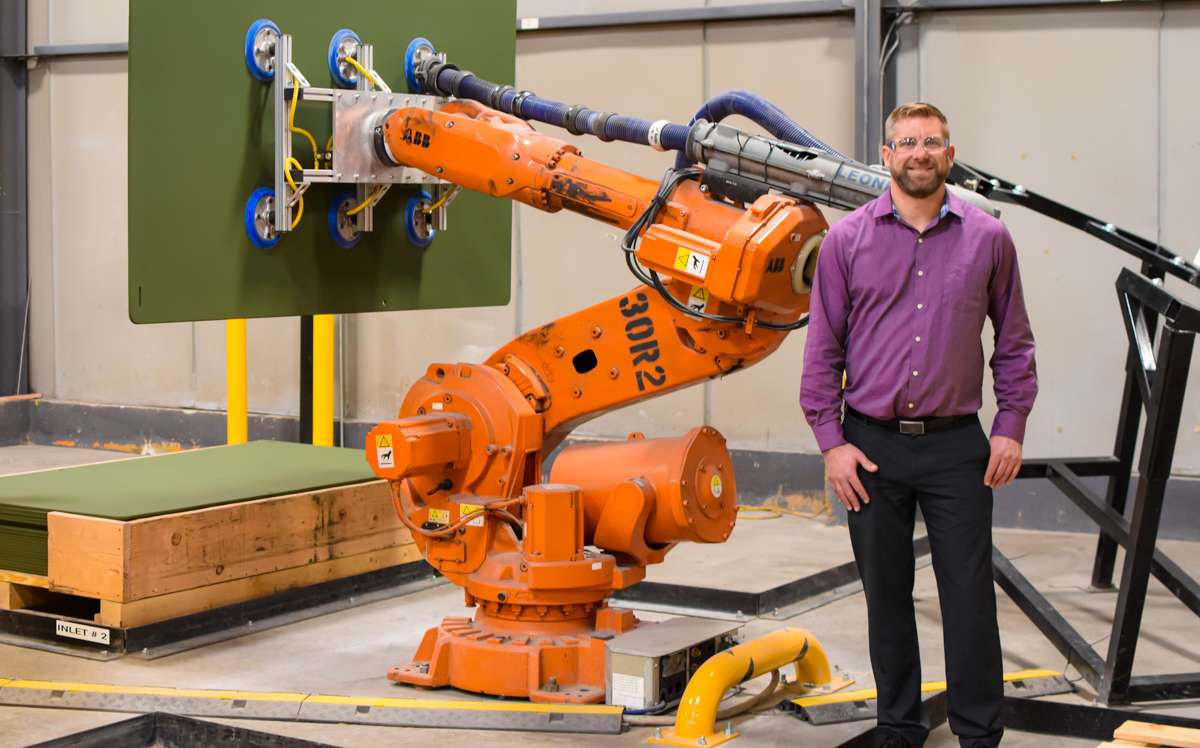
Please do not leave this page until complete. This can take a few moments.
Several years ago, Bristol Seafood began to automate operations to accommodate its growing wholesale and ready-to-cook retail lines.
“It helps our team create more product with the same number of people,” says President and CEO Peter Handy.
For example, a waterjet X-ray machine inspects and portions filets at speeds a human can’t.
“We get a level of product precision and specificity that can’t be accomplished by hand,” Handy says.
Another advantage? Automation eliminates tasks that just aren’t satisfying.
“One thing we do that’s tricky is make boxes of fish weigh exactly 10 pounds,” he says. “That sounds pretty straightforward in theory.”
But filets come in different weights. What’s the right combination? Previously, Handy’s team weighed filets individually. Now a batching system weighs and conveys every filet automatically to waiting boxes.
“Before, we couldn’t get exactly 10 pounds. Now we can,” he says.
More companies are looking to automated systems to speed operations, grow capacity, and in some cases fill in for workers they can’t find.
“Companies have been implementing new technologies and new automation into their plants over the past 15 to 20 years for many reasons,” says Lisa Martin, executive director of the Manufacturers Association of Maine in Portland. “It’s a result of, ‘We can do this faster, cleaner and easier.’ But also a result of the changing technologies of the modern world of manufacturing.”
How automated can automation be?
“Automation is all in the eye of the user and/or company,” says Bob Kuniega, president and CEO of Lanco Integrated in Westbrook. “It really is about a cost benefit analysis, weighing manual processes against more automated ones. Manual processes inherently have a higher labor content versus automated ones, requiring more upfront capital investments to offset applied labor hours.”
Lanco makes robotic systems for clients to perform mass product assembly and tests. Kuniega notes the terms “robots” and “automation” are not equivalent. Robots are a component tool, like other items such as imaging, digitization of data and artificial intelligence.
“Automation is the thoughtful integration of various tools to improve a process outcome,” he says.
The result? Improved throughput, enhanced quality, scrap reduction, worker safety and reduced cost.
Kuniega notes the technology poses challenges.
“The replacement of manual operations with more automated ones will require workforce retraining and in many cases additional schooling,” he says. “These new roles required to monitor and run various pieces of equipment will need enhanced analytic skills, structured programming familiarity, etc., to optimize and troubleshoot these machines.”
On the other hand, he continues, “The benefit to the employee is that dirty, dull, dangerous and difficult can be reduced or eliminated. Employees who are creating and running these machines are much more engaged leading to a more fulfilling work environment.”
“There’s definitely a learning curve,” says Handy.
Handy notes automation is an iterative process — one piece of equipment or process at a time.
“Figuring out the right degree of automation to put into place is a constant thought process that’s driven by the question, ‘Will this help us make a better product, will it make jobs more interesting, will it support our growth?’” he says.
Once the decision is made, he explains to the team what to expect.
“First it shows up on the loading dock and everyone looks at it and says, ‘This is way bigger than we thought and it’s not going to fit,’” he describes. “Then we move it in and it fits. Then we set it up and it doesn’t work right and we reach a point of frustration and everyone says, ‘Maybe it fits, but there’s no way it’s going to work.’
"Then we get it working and it works for a while, but then it breaks, and then people say, ‘It’s more trouble than it’s worth.’ Then eventually we learn how to fix it, because machines break in a dozen ways and the best way to fix it is to learn how to fix it. Then people go, ‘Oh my gosh, how did we ever live without this?’ And then when we love that piece of equipment, another piece of equipment shows up at the loading dock.”
He adds, “I thought we’d do that once or twice and then we’d develop faith in the process. But we go through the same thing every single time.”
Top reasons driving adoption of automation include production consistency and better employee utilization, says John Belding, director of the University of Maine’s Advanced Manufacturing Center, an outreach economic development arm assisting companies with advanced technology.
“It’s a great opportunity to take that employee and move them into a much more important role,” Belding says.
Investment in automation, he estimates, can range from $30,000 to $500,000, partly depending on the level of customization.
Starting in 2020, Compotech in Brewer has invested hundreds of thousands of dollars into automated systems that integrates six robots to create ballistic protection systems and expeditionary shelters for the U.S. Army.
“We’re using automation throughout the production line,” says the company’s president, Paul Melrose.
The Advanced Manufacturing Center helped Compotech automate its process for molding 4-foot by 7-foot ballistic protection panels. Massive Six-axis robotic arms — with a range of motion similar to the human arm — are used to sand, drill, weld and package the panels.
“It really increases our overall manufacturing efficiency,” says Melrose. “The robots are great for doing repetitive tasks.”
The robots effortlessly lift and move as much as 500 pounds and easily process stacks of armor panels by accurately position them for precision drilling, sanding and labeling operations. Another robotic cell at Compotech is used to weld steel hardware, providing repeatable parts with consistency quality.
Swapping in robots to perform heavy and repetitive tasks is not something employees should be alarmed by, says Melrose.
“It is a strenuous job to manually stack armor panels all day,” he says. “The job is very repetitive, and it is hard on your body. So we use automation to replace jobs that could have a high risk of injury that no one should be wanting to do. The new jobs created are robot operator and engineering jobs that provide higher wages to our employees compared to manual labor jobs.”
Precision and higher throughput are key to the company’s growth.
“Some of our machines can process a months’ worth of product in three days’ time,” he says.
Franklin Printing in Farmington last year acquired a $1.25 million, 60-foot-long by 15-foot-wide variable, high-speed press. Additional investments of $1.25 million were made in separate but integrated machines that can cut, fold, collate and staple.
“If someone wanted us to print a million postcards for them, we could print them and put a million different addresses on them as they’re going through the press,” says the company’s general manager, David Nemi.
The investments in the printer and related equipment have meant that medical supply companies, pop-up clinics, health care firms and other businesses have been able to print labels, signage and packaging quickly.
That need became particularly apparent over the past year, when medical product manufacturers in Maine and beyond have needed fast, flexible and accurate materials.
The technology allows for more production flexibility and labor efficiency.
“We have one operator running the press,” he says. That compares with the company’s traditional sheet fed presses, which require two people to run.
Variable printing at high speeds and digital accuracy mean that every square inch can be unique. On a conventional press, those million postcards would be printed on one side, then go through another machine to print addresses on the other side. Now the operations are condensed into one pass.
“The automation allows us to increase capacity without increasing the workforce, which has proven over the last several months to be beneficial to us because we’ve had challenges finding workers to join our team as we’ve been growing,” says Nemi.
Automated workflow allows two people to carry out operations previously occupying five or more.
Automation at Possum Hollow Farm Soap allows the company of five employees to perform full wraps — the way a present is wrapped — of individual soaps.
The Wells-based organic skin care company has its manufacturing plant in Sanford.
The system, developed with Advanced Manufacturing Center’s help and adopted in 2017, pares a day of labor to a couple of hours, says co-owner Derek Bedford.
An automated air cutter cuts over 100 bars of soap in less than five minutes, compared with hand-cutting by two people, in 20-25 minutes.
Automation has been great for reducing physical stress, he says.
“Automation makes things easier, faster, and it just allows your company to expand and do more R&D,” Bedford says.
At Lanco, Kuniega notes that businesses that have implemented “robust technology solutions have improved their throughput, quality, reduced their inventory, and mitigated hiring challenges through automation. These are all positive results for their business and their customers.”
For the workplace, he cautions, a common fallacy it that automation reduces the need for workers.
“Quite the contrary,” he says. “In many cases, very difficult task for humans to manually accomplish are automated, thus elevating the worker to more rewarding and fulfilling task within the business. Additionally, when automation is done correctly, the cost of goods is reduced, making products more accessible to a broader set of the population.”
Are workers generally receptive to automation? That can be a challenge, says Belding.
“Until you have that culture in your facility where you’re able to embrace the technology and have the training and the technician available to get those automation pieces in place, that’s the big challenge,” he says. “It’s definitely a new world for a lot of people.”
0 Comments